The most complete article about PVC marble UV board panels, here you can find the information you need!hello@FOROREE.com
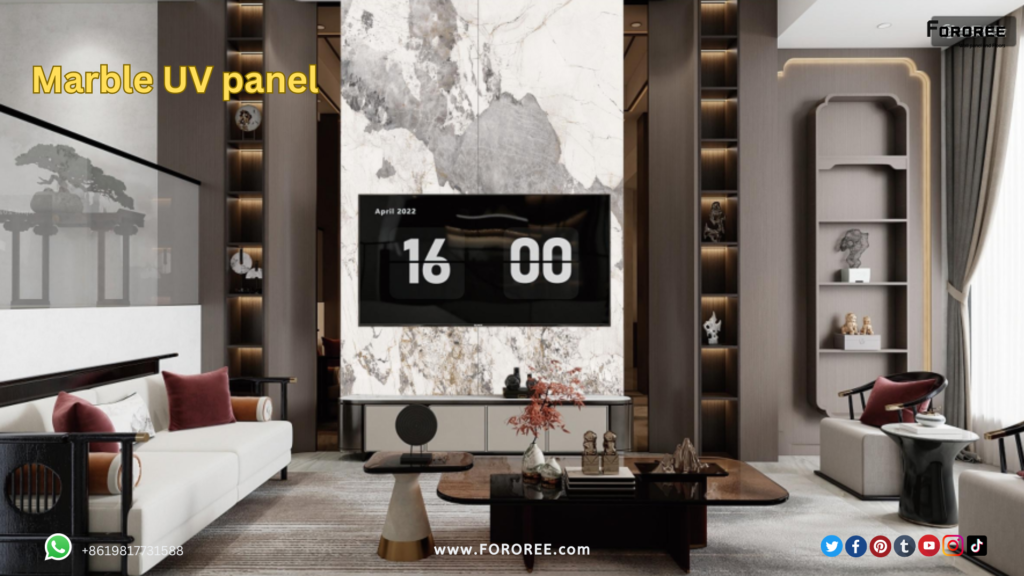
What is a UV Board Wall Panel ?
A UV board panel, commonly known as a UV-coated panel, is a type of decorative panel that is treated with a UV (ultraviolet) curing process to enhance its surface properties. This treatment involves applying a coating to the surface of the panel, which is then exposed to ultraviolet light to cure or harden the coating. This process results in a finish that is not only aesthetically appealing but also highly durable and resistant to various environmental factors. Here’s a more detailed breakdown of UV board panels:
Key Features and Characteristics
- High Gloss and Aesthetic Appeal:
- Surface Finish: UV boards often have a high-gloss finish, which gives them a shiny and reflective surface. This can add a modern and sleek look to any space.
- Color Variety: They come in a wide range of colors and designs, including solid colors, wood grain patterns, and custom graphics, making them versatile for various decorative applications.
- Durability and Resistance:
- Scratch Resistance: The UV curing process creates a hard surface that is highly resistant to scratches and abrasions, making these panels ideal for high-traffic areas or applications where surface durability is crucial.
- Stain Resistance: UV-coated panels resist stains from common household substances, making them easy to clean and maintain.
- Moisture and Heat Resistance: These panels can withstand exposure to moisture and moderate heat, making them suitable for use in kitchens and bathrooms.
- Environmental and Health Benefits:
- Low Emissions: UV coatings are often low in volatile organic compounds (VOCs), making them more environmentally friendly and safer for indoor use compared to some other types of coatings.
- Anti-Bacterial Properties: Some UV-coated panels have anti-bacterial surfaces, which can help maintain hygiene in spaces like hospitals and kitchens.
- Versatility in Applications:
- Interior Design: UV boards are widely used in residential and commercial interiors for wall cladding, cabinetry, furniture, and decorative panels.
- Retail and Commercial Spaces: Their high gloss and customizability make them popular in retail displays and commercial interiors.
- Signage: Due to their durability and ability to hold vibrant colors, UV boards are also used for creating signs and displays.
Manufacturing Process
The production of UV board panels typically involves the following steps:
- Base Material Preparation:
- The base material, which can be MDF (medium-density fiberboard), HDF (high-density fiberboard), plywood, or other substrates, is prepared and cut to the desired dimensions.
- Surface Coating Application:
- A UV coating material is applied to the surface of the panel. This coating can be clear or pigmented, depending on the desired final appearance.
- UV Curing:
- The coated panel is then exposed to ultraviolet light. The UV light causes the coating to harden or cure rapidly, creating a durable and smooth finish. This process typically takes only a few seconds.
- Final Finishing:
- After curing, the panels may undergo additional finishing processes, such as sanding or polishing, to achieve the desired level of gloss and smoothness.
Advantages of UV Board Panels
- Enhanced Aesthetics: The high-gloss finish of UV panels enhances the visual appeal of any space, giving it a luxurious look.
- Superior Durability: The UV curing process makes these panels highly resistant to wear and tear, extending their lifespan and maintaining their appearance over time.
- Easy Maintenance: The smooth, non-porous surface of UV panels makes them easy to clean and resistant to common stains.
- Environmentally Friendly: UV coatings are often more eco-friendly compared to traditional coatings, due to lower emissions of VOCs.
- Cost-Effective: While providing high-quality finishes and durability, UV boards can be more cost-effective than some other high-end decorative materials.
Common Uses of UV Board Panels
- Cabinetry and Furniture:
- UV boards are often used in kitchen and bathroom cabinetry due to their moisture resistance and durability. They are also popular in the manufacturing of modern, sleek furniture.
- Wall Cladding:
- These panels are used as wall coverings in both residential and commercial spaces, providing a high-gloss, stylish surface that is easy to maintain.
- Retail and Display Fixtures:
- The high-gloss and durable surface makes UV panels ideal for retail displays and fixtures that need to withstand frequent handling and cleaning.
- Interior Decoration:
- UV panels are used to create decorative elements in interiors, such as feature walls, room dividers, and custom decorative panels.
- Signage:
- Due to their durability and ability to retain vibrant colors, UV boards are often used for signage and branding purposes in both indoor and outdoor settings.
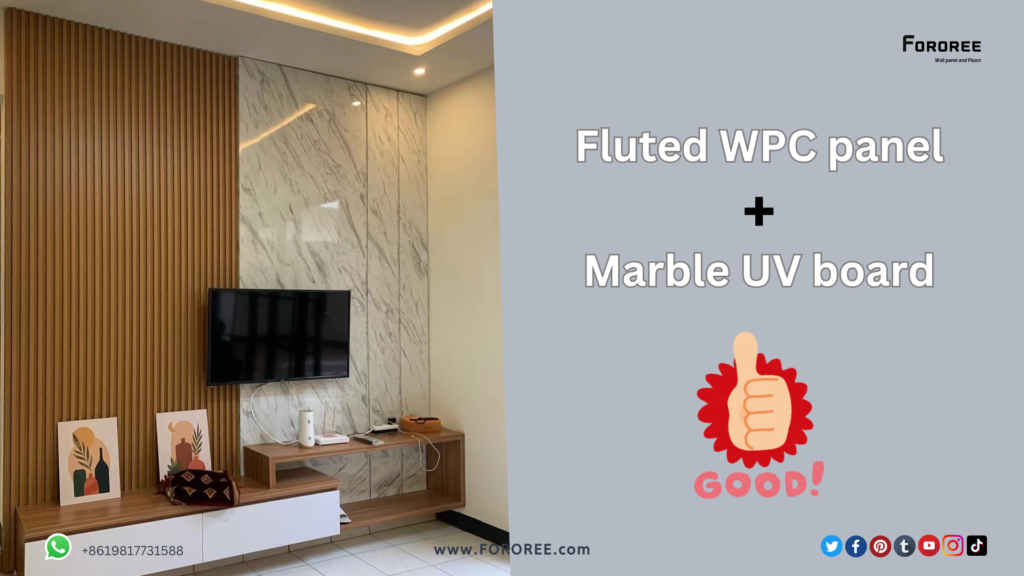
Where is the use of UV marble pvc board?
UV marble PVC board is a versatile and decorative material widely used in various applications due to its aesthetic appeal, durability, and practical benefits. Here’s a comprehensive look at its uses:
Uses of UV Marble PVC Board:
- Interior Wall Cladding:
- Residential Spaces: UV marble PVC boards are popular for covering walls in homes, particularly in living rooms, bedrooms, and hallways, where they provide a luxurious marble-like appearance without the high cost of real marble.
- Commercial Spaces: These boards are also extensively used in commercial environments such as offices, retail stores, and hotels. Their elegant finish enhances the aesthetic appeal of lobbies, conference rooms, and display areas.
- Ceiling Panels:
- UV marble PVC boards are used as ceiling panels in various settings to create a sophisticated look. They can be installed in drop ceilings or directly onto existing ceilings, providing a clean, polished finish that resembles marble.
- Kitchen and Bathroom Surfaces:
- Backsplashes: In kitchens, UV marble PVC boards serve as backsplashes behind sinks and stovetops, offering a stylish and easy-to-clean surface.
- Wall Panels in Bathrooms: They are ideal for bathroom walls, including shower areas, due to their water-resistant properties, adding a touch of elegance while being resistant to moisture and mold.
- Furniture and Cabinetry:
- Cabinet Doors and Shelves: UV marble PVC boards are used in the manufacturing of cabinet doors and shelves, giving furniture a high-gloss, marble-like finish that is both attractive and durable.
- Tabletops and Countertops: They can be used as surfacing materials for tabletops and countertops, providing a sleek, modern look that is easy to maintain and resistant to scratches and stains.
- Partitions and Room Dividers:
- UV marble PVC boards are employed in creating room dividers and partitions in open-plan spaces, offering a decorative element that also provides privacy and defines different areas within a larger room.
- Retail Display Units:
- In retail settings, these boards are used to construct display units and shelves, enhancing product presentation with a premium look that mimics real marble.
- Hospitality Industry:
- Hotels and Restaurants: In the hospitality sector, UV marble PVC boards are used for wall cladding, countertops, and decorative elements, creating an upscale atmosphere that appeals to guests.
- Spa and Wellness Centers: Their water-resistant and easy-to-clean properties make them suitable for use in spas and wellness centers.
- Exhibition and Trade Show Booths:
- UV marble PVC boards are utilized to create visually appealing and durable exhibition booths and display stands. Their lightweight nature allows for easy installation and transport, which is essential for temporary setups.
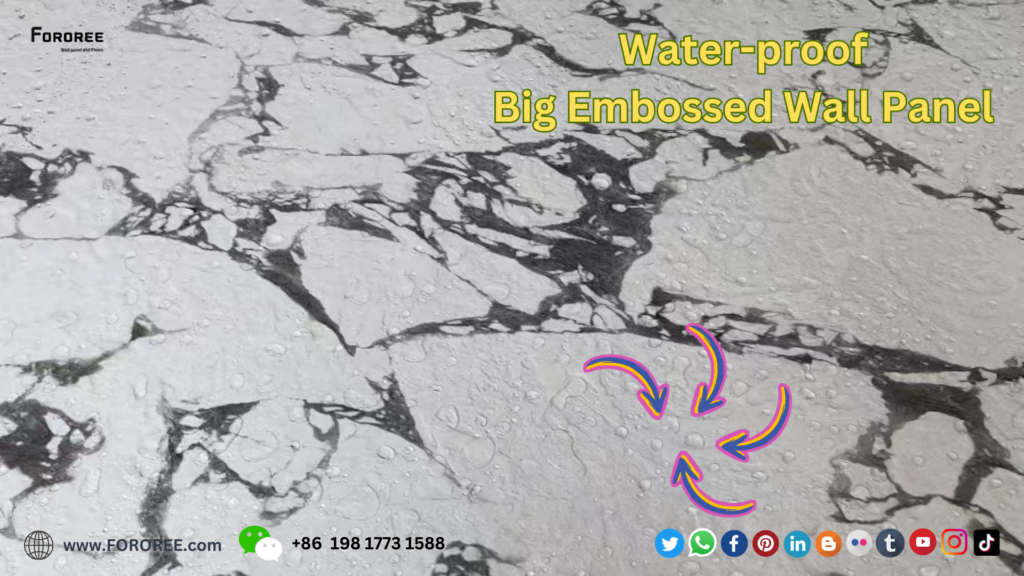
Does UV marble wall Panels Waterproof ?
UV panels, also known as UV-coated panels, are highly regarded for their aesthetic appeal and durability. However, when it comes to being waterproof, the answer is nuanced and depends on the context and specific use case. Here’s a detailed look at how UV panels handle water exposure:
Water Resistance vs. Waterproof
- Water Resistance:
- Surface Coating: The UV coating on the panel provides a high degree of water resistance. This means that the surface of the panel can withstand exposure to water and moisture without significant damage. The coating prevents water from penetrating into the panel’s surface, making it suitable for environments where occasional or incidental contact with water occurs.
- Applications: This water-resistant property makes UV panels ideal for use in kitchens, bathrooms, and other areas where they might be exposed to splashes, steam, or high humidity. They are also easy to clean and maintain in such settings.
- Waterproof:
- Substrate Material: The core material or substrate of the panel plays a crucial role in determining its overall water resistance. Common substrates like MDF (Medium-Density Fiberboard), HDF (High-Density Fiberboard), and plywood are not inherently waterproof. Prolonged or significant exposure to water can cause these materials to swell, warp, or deteriorate over time.
- Limitations: Even with a UV-resistant surface, if the panel is submerged in water or exposed to heavy moisture over an extended period, the substrate can absorb water, leading to damage. Thus, while the UV coating is water-resistant, the panel as a whole is not entirely waterproof unless it is specifically designed with a waterproof core or additional protective measures.
Enhancing Water Resistance
For applications where panels will be exposed to more substantial water contact, additional treatments or materials can enhance their water resistance:
- Waterproof Core Materials:
- PVC or Composite Cores: Panels with cores made from PVC (Polyvinyl Chloride) or composite materials are inherently waterproof. When combined with UV coatings, these panels offer superior water resistance, making them suitable for areas with high moisture exposure, such as showers or exterior applications.
- Edge Sealing:
- Edge Protection: The edges of the panels are often vulnerable to water penetration. Sealing the edges with waterproof adhesives or trims can significantly enhance the overall water resistance of the panel, protecting the core from moisture ingress.
- Full Panel Coating:
- Back and Edge Coating: Some manufacturers offer UV panels with full coatings on all sides, including the back and edges. This provides a more comprehensive moisture barrier, protecting the panel even if it’s exposed to water from multiple angles.
Practical Considerations
- Usage Areas:
- Indoor Use: For most indoor applications, UV panels offer sufficient water resistance to handle routine cleaning and exposure to moisture. They are well-suited for kitchen backsplashes, bathroom walls, and furniture surfaces.
- Outdoor Use: For outdoor or highly wet environments, it’s essential to use panels designed for such conditions. UV panels with waterproof cores or additional protective treatments are better suited for these applications.
- Maintenance:
- Care and Cleaning: Regular cleaning with non-abrasive, damp cloths will help maintain the water-resistant properties of the UV-coated surface. Avoid soaking the panels or using harsh chemicals that could degrade the UV coating or underlying material.
- Installation Considerations:
- Proper Sealing: Ensuring that panels are correctly installed with appropriate sealing at joints and edges is crucial in maintaining their water resistance over time. This prevents water from seeping into the substrate and causing damage.
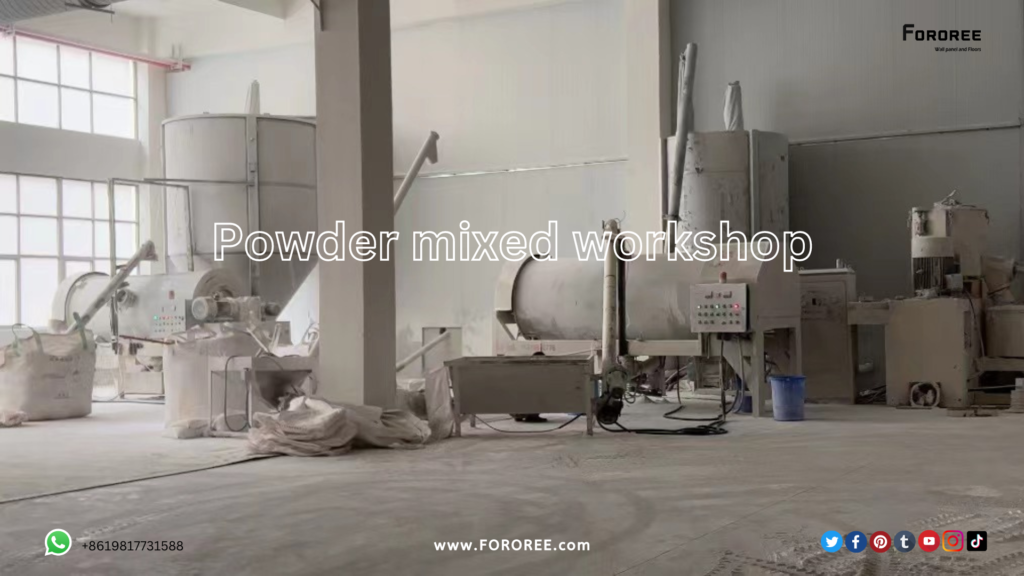
What materials used in the uv board panel ?
Materials Used in UV Board Panels
UV board panels, also known as UV-coated panels, are composite materials renowned for their high gloss finish, durability, and resistance to scratches and moisture. The construction of UV board panels involves several layers and materials, each contributing to the overall performance and appearance of the panel. Here’s a breakdown of the typical materials used in the construction of UV board panels:
1. Core Materials
The core provides the structural foundation of the panel. Common core materials include:
- MDF (Medium-Density Fiberboard):
- Description: Made from wood fibers bonded with resin under heat and pressure.
- Characteristics: Smooth, dense, and uniform. Offers good machinability and is commonly used for indoor applications.
- Applications: Ideal for furniture, cabinetry, and interior wall panels due to its stability and ease of finishing.
- HDF (High-Density Fiberboard):
- Description: Similar to MDF but denser and stronger.
- Characteristics: Provides a higher strength-to-weight ratio than MDF, making it suitable for more demanding applications.
- Applications: Used where extra durability is required, such as in flooring and high-traffic areas.
- Plywood:
- Description: Constructed from thin layers of wood veneers glued together with adjacent layers having their wood grain rotated up to 90 degrees.
- Characteristics: Strong and flexible. More resistant to warping and shrinking compared to MDF or HDF.
- Applications: Suitable for both indoor and outdoor use, making it a versatile option for various construction and furniture projects.
- Particle Board:
- Description: Made from wood chips and sawdust bonded together with a synthetic resin.
- Characteristics: Less dense and less expensive than MDF or HDF, but also less strong and durable.
- Applications: Often used in low-cost furniture and interior applications where heavy load-bearing is not required.
- PVC (Polyvinyl Chloride) or Composite Materials:
- Description: Synthetic core materials that provide excellent water resistance and durability.
- Characteristics: Lightweight, waterproof, and resistant to corrosion. PVC panels are particularly popular for environments with high moisture exposure.
- Applications: Ideal for kitchen and bathroom applications, as well as exterior cladding and other areas prone to moisture.
2. Surface Layer
The surface layer of UV board panels is what gives them their distinctive high gloss and protective qualities. This layer typically consists of:
- UV Coating:
- Description: A clear, protective layer applied to the surface of the panel. It is cured using ultraviolet (UV) light, which hardens the coating and bonds it to the panel.
- Characteristics: Provides a high-gloss finish, excellent scratch resistance, and enhanced durability. UV coatings are also resistant to yellowing and maintain their clarity over time.
- Applications: Used in areas that require a high degree of cleanliness and visual appeal, such as kitchen cabinets, bathroom vanities, and high-end furniture.
- Decorative Film or Veneer:
- Description: A layer of decorative material (such as paper, PVC, or wood veneer) that provides the panel with its visual appearance. This layer is often placed beneath the UV coating.
- Characteristics: Offers a wide range of design options, including wood grain patterns, solid colors, and textured finishes. The film or veneer determines the aesthetic appeal of the panel.
- Applications: Used in applications where appearance is crucial, such as wall panels, office partitions, and decorative furniture surfaces.
3. Adhesives and Bonding Agents
To ensure the various layers of the UV board panel are securely bonded, high-quality adhesives are used:
- Urea-Formaldehyde Resin:
- Description: Commonly used adhesive for bonding wood fibers in MDF and particle board.
- Characteristics: Provides strong bonding but may release formaldehyde gas, which can be a concern for indoor air quality.
- Applications: Frequently used in the manufacturing of MDF and particle boards.
- Melamine Formaldehyde Resin:
- Description: A durable, heat-resistant adhesive often used in high-quality panels.
- Characteristics: Offers excellent moisture resistance and is used in panels designed for high humidity environments.
- Applications: Used in the production of panels that need enhanced moisture resistance, such as kitchen and bathroom panels.
- Polyurethane (PU) Adhesive:
- Description: Provides a strong, water-resistant bond suitable for various substrates.
- Characteristics: Versatile and durable, making it ideal for panels exposed to moisture or requiring robust adhesion.
- Applications: Used for bonding different types of cores and decorative layers, especially in environments with variable moisture levels.
4. Edge Banding and Finishing Materials
To protect and enhance the edges of the UV board panels, edge banding is often applied:
- PVC Edge Banding:
- Description: A strip of PVC material applied to the edges of the panel.
- Characteristics: Durable, moisture-resistant, and available in various colors and textures to match the panel surface.
- Applications: Commonly used in furniture and cabinetry to provide a finished look and protect the edges from damage.
- ABS Edge Banding:
- Description: Made from Acrylonitrile Butadiene Styrene, a tough and resilient plastic.
- Characteristics: Eco-friendly, recyclable, and offers good impact resistance.
- Applications: Used in high-quality furniture and panels where environmental considerations and durability are important.
How to produce pvc uv marble panel ?
Producing PVC UV marble panels involves several steps and processes that combine the properties of PVC (polyvinyl chloride) with a UV (ultraviolet) cured coating to achieve a marble-like appearance. Here’s a general overview of the production process:
1. Material Preparation:
PVC Substrate:
- The base material for PVC UV marble panels is polyvinyl chloride (PVC). PVC is a versatile plastic known for its durability, flexibility, and resistance to moisture and chemicals.
UV Coating:
- UV coating is a liquid resin applied to the PVC substrate. This coating contains additives and pigments that give the final product its desired appearance, such as the look of natural marble.
2. Production Steps:
a. Mixing and Preparation:
- The PVC material is processed into sheets or panels of desired thickness and dimensions. This involves mixing PVC resin with additives, stabilizers, and pigments in a controlled environment to achieve the desired properties and color.
b. UV Coating Application:
- The prepared PVC panels are coated with a UV-curable liquid resin mixture. This coating is applied evenly over the surface of the PVC substrate using techniques such as roll coating, curtain coating, or spray coating.
c. UV Curing:
- After the UV coating is applied, the panels pass through a UV curing chamber or conveyor system. UV lamps emit ultraviolet light that initiates a chemical reaction in the resin, causing it to cure and harden quickly. This UV curing process is essential for creating a durable and scratch-resistant surface.
d. Cooling and Quality Control:
- Once cured, the panels are cooled and undergo quality control inspections. Panels are inspected for defects such as uneven coating, color consistency, or surface imperfections. Any defective panels are identified and corrected or discarded.
3. Finishing and Packaging:
e. Cutting and Sizing:
- After passing quality control, the PVC UV marble panels are cut into specific sizes and shapes according to customer requirements or standard dimensions.
f. Packaging:
- The finished panels are packaged securely for storage, transportation, and distribution to customers or retailers. Packaging ensures the panels are protected from damage during handling and shipping.
Additional Considerations:
- Design Flexibility: Manufacturers can create a variety of designs and patterns by adjusting the composition of the UV coating, including different colors, textures, and effects to mimic natural marble or other materials.
- Environmental Considerations: PVC UV marble panels are typically manufactured with considerations for environmental impact, such as using recycled materials or ensuring compliance with environmental regulations for manufacturing processes and waste disposal.
Does uv board panel ECO friendly ?
Is UV Board Panel Eco-Friendly?
The eco-friendliness of UV board panels depends on several factors, including the materials used in their construction, the manufacturing process, and their lifecycle. Let’s examine these aspects in detail to understand the environmental impact and eco-friendliness of UV board panels.
Key Factors Influencing Eco-Friendliness
- Core Materials
- MDF (Medium-Density Fiberboard) and HDF (High-Density Fiberboard):
- Eco-Friendliness: MDF and HDF are made from wood fibers, often sourced from recycled or by-product wood materials. This makes them a more sustainable option compared to solid wood. However, they can contain formaldehyde-based resins, which may release harmful emissions.
- Sustainability: If sourced from sustainably managed forests or recycled materials, they contribute positively to environmental sustainability.
- Plywood:
- Eco-Friendliness: Plywood uses thin layers of wood veneers, which can be sourced from sustainable forests. Its use of wood is generally more efficient than solid wood panels.
- Sustainability: Plywood can be eco-friendly if the wood is harvested responsibly and the adhesive used is low in harmful chemicals.
- Particle Board:
- Eco-Friendliness: Often made from wood waste and by-products, particle board reduces waste and can be considered a more sustainable option if the resins used are low in formaldehyde.
- Sustainability: Like MDF and HDF, particle board’s eco-friendliness depends on the source of the wood and the type of adhesive used.
- PVC or Composite Cores:
- Eco-Friendliness: PVC is a plastic material derived from petroleum, making it less eco-friendly due to its non-renewable source and production process. However, it is highly durable and recyclable, which can offset some environmental concerns.
- Sustainability: Composite materials, including PVC, should ideally be recycled to reduce their environmental footprint.
- MDF (Medium-Density Fiberboard) and HDF (High-Density Fiberboard):
- Surface Coating
- UV Coating:
- Eco-Friendliness: UV coatings are cured using ultraviolet light, which typically involves less energy and fewer volatile organic compounds (VOCs) than traditional coatings. This makes the process relatively eco-friendly.
- Sustainability: The UV coating itself is durable and enhances the lifespan of the panel, reducing the need for frequent replacements and contributing to sustainability.
- UV Coating:
- Adhesives and Bonding Agents
- Types of Adhesives:
- Formaldehyde-Based Adhesives: Commonly used in MDF, HDF, and particle board, these can release VOCs that are harmful to the environment and human health.
- Low-VOC and Formaldehyde-Free Adhesives: Increasingly, manufacturers are moving towards using safer adhesives that have minimal environmental impact.
- Eco-Friendliness: The use of low-VOC or formaldehyde-free adhesives significantly enhances the eco-friendliness of the panels.
- Types of Adhesives:
- Manufacturing Process
- Energy Use and Emissions:
- Eco-Friendliness: The manufacturing process for UV board panels can vary in its energy consumption and emissions. Processes that use renewable energy sources and minimize emissions are more eco-friendly.
- Waste Management:
- Sustainability: Effective waste management and recycling of manufacturing by-products can improve the sustainability of the production process.
- Energy Use and Emissions:
- End-of-Life Considerations
- Recyclability:
- Eco-Friendliness: UV board panels made from recyclable materials and using recyclable adhesives can be more eco-friendly at the end of their lifecycle.
- Disposal: Panels that are not easily recyclable or that release harmful substances when disposed of are less eco-friendly.
- Recyclability:
Conclusion
UV board panels can be eco-friendly, particularly when they are produced using sustainably sourced materials, low-VOC adhesives, and energy-efficient manufacturing processes. Their durability and resistance to damage contribute to a longer lifespan, which can reduce the need for frequent replacements and thus lower their overall environmental impact.
Choosing eco-friendly UV board panels involves considering factors such as:
- The source and type of core materials.
- The use of environmentally friendly adhesives.
- The efficiency and cleanliness of the manufacturing process.
- The recyclability and disposal options at the end of their life.
When selecting UV board panels, it’s beneficial to look for certifications or labels that indicate compliance with environmental standards, such as FSC (Forest Stewardship Council) for wood products, or low-VOC certifications for adhesives and coatings. This ensures that the panels meet certain criteria for eco-friendliness and sustainability.
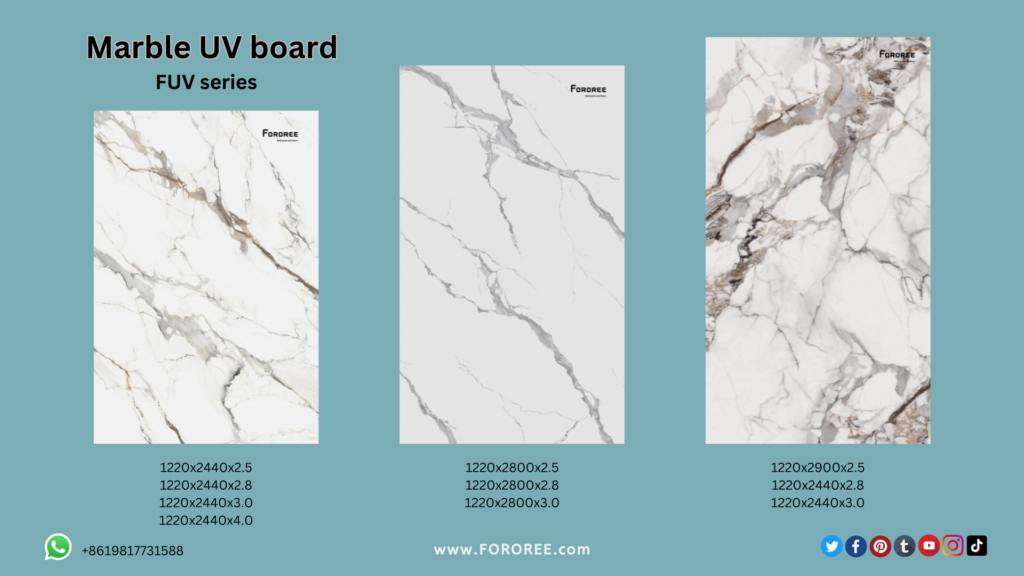
What’s the size of the uv board panel ?
The size of UV board panels can vary widely depending on their intended use and the manufacturer. However, there are standard dimensions that are commonly produced to meet the requirements of various applications such as cabinetry, furniture, wall panels, and interior decorations. Here’s a breakdown of the typical sizes for UV board panels:
Standard Sizes
- Sheet Dimensions
- 4 feet x 8 feet (1220 mm x 2440 mm):
- This is the most common size for UV board panels, used extensively in furniture making, cabinetry, and interior wall panels.
- 4 feet x 9 feet (1220 mm x 2745 mm):
- This slightly longer size is also popular and is used for larger projects requiring fewer seams.
- 4 feet x 10 feet (1220 mm x 3050 mm):
- Less common but available for applications needing even longer lengths.
- 4 feet x 8 feet (1220 mm x 2440 mm):
- Thickness
- 2 mm to 3 mm:
- UV board panels come in various thicknesses depending on the specific application.
- 2 mm to 3 mm:
Custom Sizes
Many manufacturers offer custom sizing to cater to specific project requirements. Custom sizes are particularly useful in large-scale construction or bespoke furniture design where non-standard dimensions are needed to minimize waste and enhance aesthetics.
Specialized Sizes
- Small Panels
- 2 feet x 4 feet (610 mm x 1220 mm):
- Used for smaller projects, sample purposes, or where ease of handling and transport is important.
- 2 feet x 4 feet (610 mm x 1220 mm):
- Large Panels
- 5 feet x 10 feet (1525 mm x 3050 mm):
- For larger surfaces requiring fewer joints, such as large cabinet doors or expansive wall cladding.
- 5 feet x 10 feet (1525 mm x 3050 mm):
Applications and Corresponding Sizes
- Cabinetry and Furniture:
- Typically use standard 4 feet x 8 feet panels with thicknesses ranging from 12 mm to 18 mm, providing the necessary strength and stability.
- Wall Panels and Interior Decorations:
- Often use thinner panels (6 mm to 12 mm) and standard or larger sizes (up to 4 feet x 10 feet) to cover large areas smoothly and efficiently.
- Commercial and Retail Spaces:
- Custom sizes and thicker panels (up to 25 mm) may be used to create durable and visually appealing fixtures and fittings.
Is there any protective film on the surface of the marble UV panel ?
Yes, PVC UV marble panels often come with a protective film on their surface. This film serves several important purposes during transportation, handling, and installation. Here’s a detailed look at the role of the protective film on these panels:
Purpose of the Protective Film:
- Surface Protection:
- Prevents Scratches: The protective film shields the delicate surface of the panel from scratches and abrasions that can occur during handling, transportation, and installation.
- Guards Against Dirt and Dust: It keeps the panel clean by protecting it from dust, dirt, and other contaminants that might settle on the surface.
- Chemical and Stain Resistance: The film helps prevent staining and chemical damage that might occur from accidental spills or contact with harmful substances before the panel is installed.
- Maintains Finish:
- Gloss Retention: For high-gloss panels, the protective film preserves the shine and smooth finish until the panel is ready to be displayed or installed.
- Matte Finish Protection: For matte panels, the film helps maintain the texture and appearance, preventing fingerprints and smudges.
- Ease of Handling:
- Installation Convenience: The film makes it easier to handle the panels without directly touching the surface, reducing the risk of leaving marks or residues.
- Application Marking: During the installation process, any markings or notes can be made on the film without damaging the actual panel surface.
Application of Protective Film:
- Material:
- The protective film is typically made from a thin, transparent plastic material, like polyethylene (PE). It is designed to be strong enough to protect the panel but easy to peel off without leaving residue.
- Application Process:
- The film is usually applied during the manufacturing process immediately after the UV coating has been cured. This ensures the surface is protected from the moment it is produced.
- Thickness and Adhesion:
- The film’s thickness is carefully chosen to provide adequate protection without being too thick or cumbersome. The adhesive used is designed to be strong enough to keep the film in place but gentle enough to be removed easily.
Removing the Protective Film:
- Peel-Off Process:
- The film is designed to be peeled off smoothly and easily. It should be removed after the panel has been installed and before the final cleaning and inspection.
- No Residue:
- A quality protective film will leave no adhesive residue on the panel’s surface, ensuring a clean, polished appearance once it is removed.
- Timely Removal:
- It’s recommended to remove the film as soon as the installation is complete and the environment is clean to avoid any adhesive bonding issues that can occur if the film is left on for an extended period.
Practical Considerations:
- Check Before Installation: Always check for the presence of a protective film before handling the panels to ensure it is intact and properly applied.
- Remove Carefully: Use care when removing the film to avoid any sudden tearing or stretching that could leave fragments on the surface.
- Inspect Post-Removal: After removing the film, inspect the panel for any signs of damage or residue and clean the surface if necessary.
Does the surface fim could be customized to customer’s LOGO ?
Yes, the surface film on PVC UV marble panels can often be customized with a customer’s logo or branding. This customization is usually part of the packaging and branding services offered by the manufacturer or supplier. Here’s how the process typically works and what you can expect:
Customization Process:
- Design Submission:
- The customer provides the manufacturer with the desired logo, branding details, or design specifications. This usually includes high-resolution images or vector files of the logo, along with any specific placement and size requirements.
- Film Production:
- The manufacturer works with film suppliers to produce the protective film featuring the custom logo. This process may involve:
- Printing: The logo is printed onto the protective film using high-quality printing techniques. This ensures the logo appears clearly and accurately on each panel.
- Embossing or Marking: In some cases, the logo might be embossed or marked onto the film, depending on the desired effect and the type of protective film used.
- The manufacturer works with film suppliers to produce the protective film featuring the custom logo. This process may involve:
- Application to Panels:
- Once the custom protective film is produced, it is applied to the panels during the manufacturing process. The film is usually applied right after the UV coating process to ensure the panel’s surface is protected immediately.
- Quality Check:
- Panels with the custom film undergo a quality check to ensure that the logo is correctly positioned and that the film adheres properly without defects.
Benefits of Customizing the Protective Film:
- Brand Recognition:
- Custom logos on the protective film help reinforce the customer’s brand identity, making it immediately recognizable during transportation, storage, and installation.
- Enhanced Professionalism:
- Custom branding on the protective film can enhance the perceived quality and professionalism of the product, giving customers confidence in the supplier.
- Anti-Counterfeiting:
- Custom logos can also serve as a security measure to prevent counterfeiting. It helps in verifying the authenticity of the panels and ensures that the product is genuine.
- Marketing and Promotion:
- Having a logo on the protective film can be an additional marketing tool. It ensures that every time the panel is handled or installed, the brand is prominently displayed.
Considerations for Customization:
- Cost:
- Custom printing or embossing on the protective film may add to the overall cost of the panels. It’s essential to discuss pricing with the manufacturer and consider whether the branding benefits outweigh the additional costs.
- Minimum Order Quantity (MOQ):
- Manufacturers often have a minimum order quantity for customized films. This is because producing custom-branded films typically involves setup costs that are only feasible for larger orders.
- Lead Time:
- Customization might increase the production time. Planning ahead and coordinating with the manufacturer is crucial to meet project deadlines.
- Design and Compliance:
- The design of the custom logo or branding must comply with the manufacturer’s specifications for size, color, and placement to ensure proper application and visibility on the film.
Implementation:
- Contact Manufacturer:
- Reach out to the manufacturer or supplier to discuss the possibility of customizing the protective film with your logo. Provide them with your design and any specific requirements.
- Review Samples:
- Ask for samples or proofs of the custom film to review before full production begins. This allows you to ensure the logo appears as desired and meets your quality standards.
- Approve Design:
- Once the sample is approved, the manufacturer can proceed with full-scale production of the panels with the custom protective film.
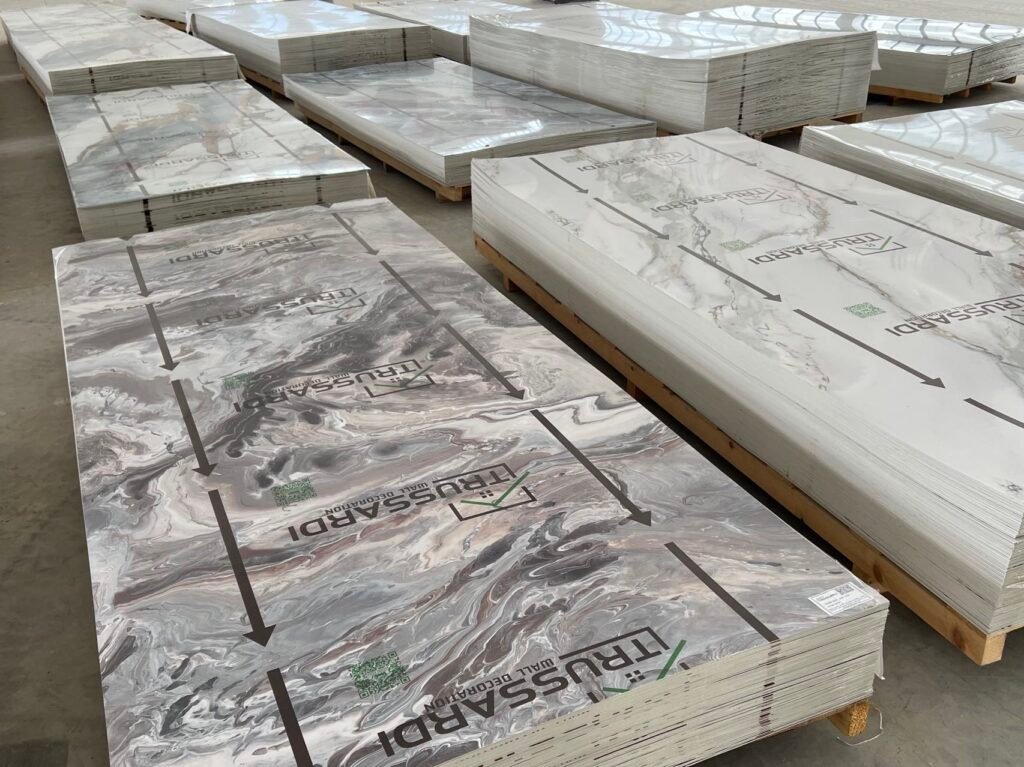
How much cost if customized the LOGO on the UV board surface film?
If use customers logo, might charge extra approx $0.035/sqm.
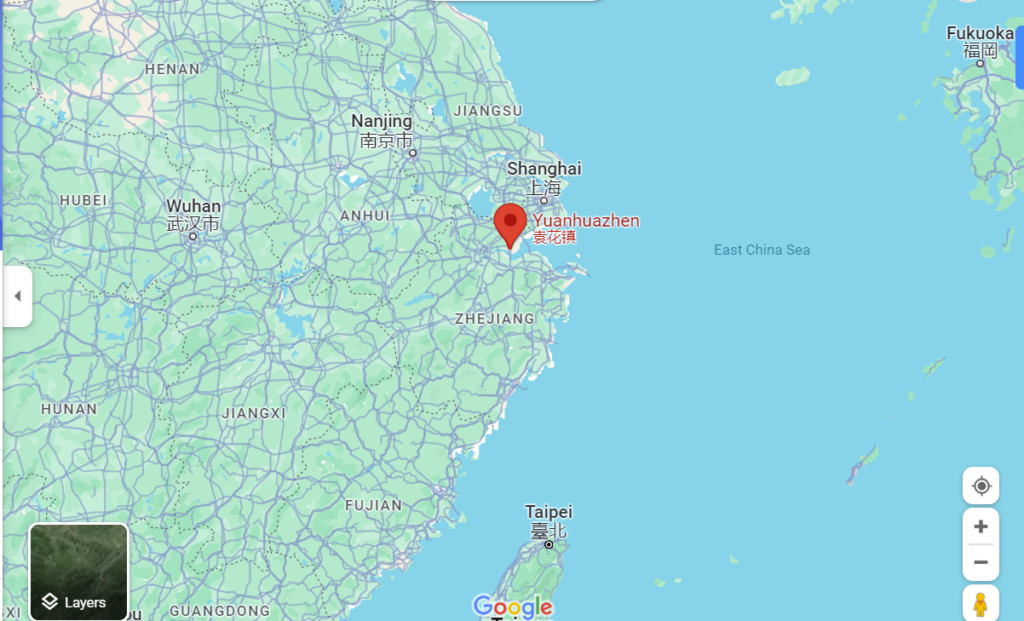
Where is the pvc uv board panel production base ?
The production base for PVC UV board panels is concentrated in several key regions worldwide, with significant hubs in China, India, and Europe. These regions have developed advanced manufacturing capabilities and infrastructure to support the large-scale production of these panels. Here’s a breakdown of the primary production bases:
1. China
China is the largest producer and exporter of PVC UV board panels, with several provinces and cities known for their extensive manufacturing facilities and industry clusters.
- Guangdong Province:
- Foshan: Known as a major center for building materials and home decor products, Foshan hosts numerous factories specializing in PVC UV board panels.
- Shunde: Part of the Foshan metropolitan area, Shunde is another significant hub with a strong focus on furniture and interior decoration materials, including PVC UV boards.
- Zhejiang Province:
- Haining: This city is renowned for its technological advancements and manufacturing capabilities, with several companies producing high-quality PVC UV boards.FOROREE is one of the supplier, 180km(approx 2 hours) from haining to yiwu.
- Yiwu: Known for its diverse industrial base, Taizhou is a significant center for the production of plastic products, including PVC UV panels.
- Shandong Province:
- Linyi: Often referred to as the “capital of panels,” Linyi is a key player in the production of various types of boards and panels, including PVC UV boards.
- Shanghai:
- As a major economic and shipping hub, Shanghai is home to many companies that manufacture and distribute PVC UV panels, catering to both domestic and international markets.
2. India
India is emerging as a significant producer of PVC UV board panels, with several regions investing in manufacturing infrastructure to meet both local and global demand.
- Maharashtra:
- Mumbai: As the financial capital, Mumbai has a growing number of manufacturers focusing on innovative building materials, including PVC UV panels.
- Gujarat:
- Ahmedabad and Surat: These cities are known for their industrial growth and have several factories producing PVC UV boards.
- Tamil Nadu:
- Chennai: With its robust industrial base, Chennai is becoming a key player in the production of various building materials, including PVC UV boards.
3. Europe
Europe also hosts several production bases for PVC UV board panels, with a focus on high-quality and innovative manufacturing practices.
- Germany:
- Renowned for its precision engineering and quality standards, Germany has several companies producing top-tier PVC UV panels, catering to the European and global markets.
- Italy:
- Italy’s strong tradition in design and manufacturing extends to building materials, including the production of high-quality PVC UV panels.
- Poland:
- Poland has a growing manufacturing sector, with several companies focusing on building materials, including PVC UV board panels.
4. Other Regions
While China, India, and Europe are the primary hubs, other regions also contribute to the production of PVC UV panels:
- Turkey: Known for its growing industrial base, Turkey has several manufacturers producing PVC UV panels for the domestic and international markets.
- Vietnam and Southeast Asia: These regions are expanding their manufacturing capabilities in various sectors, including the production of PVC UV boards, to meet the increasing demand.
Haining has how many manufacturer of pvc marble sheet?
Haining, a city in Zhejiang Province, China, is a significant hub for the production of PVC UV board panels. This area has developed into a major center for manufacturers due to its strategic location between major cities like Shanghai and Hangzhou, as well as its proximity to Yiwu, a major commodities market.
Haining’s PVC UV Panel Industry
Haining boasts a robust manufacturing base for PVC UV panels, with numerous companies operating in this sector. The city is home to over 300 manufacturers of PVC panels, many of which specialize in UV-coated products. These manufacturers produce a wide range of panels for various applications, including wall panels, ceiling panels, and decorative sheets used in residential and commercial settings.
Importance of Haining in the PVC UV Panel Market
Haining’s manufacturers are known for their capacity to produce large volumes of high-quality PVC UV panels that meet various international standards. The city’s industry benefits from:
- Strategic Location: Proximity to major cities and ports facilitates efficient logistics and export operations.
- Innovation and Quality: Companies in Haining invest significantly in research and development to enhance the quality and variety of their products.
- Competitive Pricing: Due to the high concentration of manufacturers, there is competitive pricing, which benefits both domestic and international buyers.
Contact hello@FOROREE.com or Whatsapp +8619817731588 to gather more information of UV PVC Marble Sheet Wall Panel Manufacturer !
Compare haining and shandong manufacturer, what’s the advantages and disadvantages they are
Comparing manufacturers of PVC UV panels in Haining and Shandong reveals a mix of advantages and disadvantages related to each region’s strengths, industry focus, logistics, cost structures, and technological capabilities.
Haining Manufacturers:
Advantages:
- Strategic Location:
- Proximity to Ports: Haining is strategically located near major ports like Shanghai and Ningbo, facilitating efficient logistics for both domestic distribution and international exports. This reduces shipping time and costs significantly.
- Access to Major Markets: Being close to economic hubs such as Shanghai and Hangzhou means easier access to a larger market and supply chains.
- Specialization and Expertise:
- Focus on PVC UV Panels: Haining has developed a strong specialization in PVC UV panels, leading to concentrated expertise and innovation in this area. Many manufacturers in Haining focus solely on high-gloss, decorative panels which often demand higher precision and quality.
- Advanced Manufacturing Technologies: The concentration of manufacturers in Haining has fostered a competitive environment encouraging technological advancements and process improvements in PVC UV panel production.
- Quality and Design Innovation:
- High-Quality Standards: Many companies in Haining are known for their stringent quality control measures and certifications, making their products reliable in terms of durability and performance.
- Design and Customization: Haining’s manufacturers are often more agile in responding to design trends and offer a wider range of customization options to meet specific aesthetic and functional requirements.
- Clustered Industry Ecosystem:
- Synergies and Collaborations: The dense network of suppliers and manufacturers in Haining allows for synergies, collaborations, and a supportive ecosystem which enhances the overall productivity and innovation capabilities.
Disadvantages:
- Higher Production Costs:
- Labor Costs: Being close to major urban centers like Shanghai can result in higher labor costs compared to more remote areas.
- Land and Operational Costs: The cost of land and operations in Haining is typically higher than in less developed regions, impacting overall production costs.
- Intense Competition:
- Market Saturation: The high concentration of manufacturers can lead to fierce competition, potentially reducing profit margins and making it harder for new entrants to establish themselves.
Shandong Manufacturers:
Advantages:
- Lower Production Costs:
- Cheaper Labor and Land: Shandong typically offers lower labor and land costs compared to the more industrialized regions like Haining, which can translate into lower overall production costs for manufacturers.
- Reduced Operational Expenses: The cost of utilities and other operational expenses are generally lower, contributing to more competitive pricing.
- Expansive Manufacturing Base:
- Diverse Industrial Activities: Shandong has a broad industrial base, not limited to PVC UV panels but also including a wide array of building materials. This diversity can offer advantages in terms of resource availability and cross-industry innovations.
- Large-Scale Production: Manufacturers in Shandong often operate on a larger scale, benefiting from economies of scale and the ability to fulfill large orders efficiently.
- Growing Market Access:
- Inland and Coastal Markets: Shandong’s geographical position provides access to both inland and coastal markets in China, facilitating diverse distribution networks.
- Proximity to Raw Materials: The province is close to sources of raw materials used in manufacturing, such as petrochemical products, which are essential for PVC production.
Disadvantages:
- Distance from Major Ports:
- Logistics Challenges: Although Shandong has good access to domestic markets, its distance from major international shipping ports can make international logistics more complex and costly compared to Haining.
- Technology and Specialization:
- Less Focus on High-End Products: Shandong manufacturers might not have the same level of specialization or technological advancement in high-gloss UV panels as those in Haining, potentially affecting product quality and innovation.
- Slower Adoption of New Technologies: The focus on large-scale, cost-efficient production can sometimes lead to slower adoption of the latest manufacturing technologies compared to the more innovation-driven environment in Haining.
- Environmental Regulations:
- Stricter Compliance Requirements: Shandong has faced increasing environmental regulations, which can impact manufacturing practices and add to compliance costs. This can affect operational flexibility and increase expenses related to environmental compliance.
Conclusion:
Haining’s manufacturers excel in producing high-quality, innovative PVC UV panels with a strong focus on design and customization, supported by a dense industrial network. However, this comes at the cost of higher production expenses and intense competition.
Shandong’s manufacturers benefit from lower production costs and large-scale operations, making them well-suited for mass production and cost-sensitive markets. However, they may face challenges in logistics for international shipping and in keeping pace with rapid technological advancements and niche product demands.
Both regions offer distinct advantages depending on the specific needs of buyers and the nature of the market they serve. Choosing between them involves weighing the importance of cost, quality, innovation, and logistics.
Is UV sheet can be used in the kitchen ?
Yes, UV sheets can be used in the kitchen effectively for various applications. Here are some reasons why UV sheets are suitable for kitchen use:
- Durability: UV sheets are made from durable materials such as PVC or other composite materials. They are resistant to moisture, stains, and scratches, which are common in kitchen environments.
- Easy to Clean: UV sheets have a smooth, non-porous surface that is easy to clean. Spills and splashes can be wiped off with a damp cloth and mild soap, making them ideal for kitchen backsplashes, cabinet doors, or countertops.
- Aesthetic Appeal: UV sheets come in a variety of designs, including patterns that mimic natural materials like marble or wood. They can enhance the aesthetic appeal of your kitchen while being more affordable than their natural counterparts.
- Versatility: UV sheets can be used for different kitchen applications such as wall panels, cabinet surfaces, or as a decorative element on islands or bar areas.
- Installation: They are lightweight and relatively easy to install using adhesive or mechanical fasteners. This makes them a convenient choice for kitchen renovations or updates.
- Heat Resistance: While direct heat from pots and pans should be avoided to prevent potential damage, UV sheets can withstand normal kitchen temperatures without warping or melting.
Considerations:
- Sealing: Depending on the application, you may need to seal the edges and joints of UV sheets to prevent moisture penetration, especially in areas prone to water exposure such as near sinks or behind stoves.
- Maintenance: Regular cleaning and maintenance will help preserve the appearance and longevity of UV sheets in the kitchen. Avoid abrasive cleaners or tools that could scratch the surface.
- Application: Ensure the UV sheets are installed according to manufacturer recommendations, especially if they are being used in areas where they will be exposed to moisture or heat.
Can we use UV marble sheet in the bathroom?
Yes, UV marble sheets can be used in the bathroom effectively. They are a popular choice for bathroom walls and sometimes even for shower enclosures. Here are some reasons why UV marble sheets are suitable for bathroom applications:
- Water Resistance: UV marble sheets are typically made from PVC or other plastic composites that are inherently water-resistant. This makes them suitable for environments with high humidity and moisture, such as bathrooms.
- Durability: These panels are durable and can withstand the conditions typically found in bathrooms, including occasional splashes of water and cleaning with water-based solutions.
- Easy Maintenance: UV marble sheets are easy to clean and maintain, which is beneficial in a bathroom setting where hygiene is important. Regular cleaning with mild soap and water is usually sufficient to keep them looking new.
- Aesthetic Appeal: UV marble sheets replicate the look of real marble at a fraction of the cost. They can enhance the aesthetic appeal of your bathroom, providing a luxurious and stylish appearance.
- Installation Versatility: They are lightweight and relatively easy to install, whether you choose to glue them directly to the walls or install them using mechanical fasteners.
- Variety of Designs: UV marble sheets come in a variety of designs, colors, and patterns, allowing you to achieve the desired look for your bathroom decor.
Considerations:
- Sealing: While UV marble sheets are water-resistant, it’s important to ensure that edges and seams are properly sealed to prevent water penetration and potential moisture-related issues over time.
- Ventilation: Good ventilation in the bathroom helps in maintaining the longevity of any material, including UV marble sheets. Proper ventilation reduces humidity levels and helps in drying out moisture quickly.
- Installation: Follow manufacturer guidelines for installation and ensure that any adhesive or fasteners used are suitable for bathroom environments.
How to install UV marble sheet on wall?
Installing UV marble sheets on a wall can be straightforward if you follow these general steps and tips:
1. Gather Your Materials:
- UV marble sheets
- Adhesive recommended by the manufacturer (e.g., construction adhesive suitable for PVC)
- Measuring tape
- Pencil
- Level
- Utility knife or saw (for cutting panels to size)
- Caulk gun (if using adhesive in tubes)
- Clean cloth or sponge
- Silicone caulk (optional, for sealing edges)
2. Prepare the Wall:
- Ensure the wall surface is clean, dry, and free from dust, grease, and any debris. Use a damp cloth or sponge to wipe down the surface if needed. Allow the wall to dry completely before proceeding.
3. Measure and Cut Panels:
- Measure the dimensions of the wall where you plan to install the UV marble sheets.
- Transfer these measurements onto the UV marble sheets and mark the cutting lines using a pencil.
- Use a utility knife or a saw (depending on the thickness of the panels) to cut the panels to the appropriate size. Take care to cut accurately to ensure a snug fit against adjacent panels or edges.
4. Apply Adhesive:
- Apply the adhesive to the back of the UV marble sheet according to the manufacturer’s instructions. Typically, this involves applying a generous amount of adhesive in a zigzag pattern or in beads across the back of the panel.
5. Position and Press the Panel:
- Carefully position the UV marble sheet against the wall, starting from one corner or edge.
- Press the panel firmly against the wall to ensure good contact with the adhesive. Use a level to ensure the panel is straight and aligned correctly.
6. Secure and Support:
- If necessary, use temporary supports (e.g., wooden braces or painter’s tape) to hold the panel in place while the adhesive sets. Follow the adhesive manufacturer’s recommendations for curing time.
7. Repeat for Additional Panels:
- Continue applying adhesive and installing additional UV marble sheets, ensuring each panel is snugly fit against the previous one. Use a level periodically to check for alignment.
8. Trim and Finish:
- Trim any excess adhesive or protruding edges carefully with a utility knife or scraper.
- If desired, use silicone caulk to seal the edges of the UV marble sheets, especially in areas prone to moisture (e.g., around sinks or countertops).
9. Clean Up:
- Clean any adhesive residue from the panels and surrounding areas using a suitable solvent recommended by the adhesive manufacturer.
10. Allow to Cure:
- Allow the installed UV marble sheets to fully cure according to the adhesive manufacturer’s instructions before exposing them to moisture or heavy use.
Additional Tips:
- Work systematically from one corner of the wall to ensure even installation.
- Take extra care when handling and cutting the UV marble sheets to avoid damaging the surface.
- Double-check measurements and alignments before applying adhesive to avoid mistakes.
- If installing in areas with high moisture (e.g., bathrooms), consider using a moisture-resistant adhesive and ensuring proper sealing around edges and seams.
How to clean pvc uv wall panel ?
Cleaning PVC UV wall panels is relatively simple and straightforward. Here’s a guide on how to clean them effectively:
1. Materials Needed:
- Soft cloth or sponge
- Mild soap or detergent
- Water
- Bucket or bowl for mixing cleaning solution
- Optional: Non-abrasive household cleaner suitable for PVC, if needed
2. Cleaning Steps:
- Prepare the Cleaning Solution:
- Fill a bucket or bowl with warm water.
- Add a small amount of mild soap or detergent. Avoid using harsh chemicals or abrasive cleaners as they can damage the surface of the PVC UV panels.
- Dampen the Cloth or Sponge:
- Dip a soft cloth or sponge into the cleaning solution. Wring out excess water so the cloth or sponge is damp but not dripping.
- Clean the Panels:
- Gently wipe down the PVC UV panels with the damp cloth or sponge. Start from the top of the panel and work your way downwards.
- Use light pressure to remove any dirt, dust, or stains. Avoid scrubbing vigorously, especially if the panels have a glossy finish, to prevent scratching.
- Rinse:
- Once you have cleaned the panels, rinse the cloth or sponge in clean water to remove any soap residue.
- Wipe down the panels again with the damp cloth or sponge rinsed in clean water to remove any remaining soap.
- Dry the Panels:
- Use a dry, soft cloth to wipe down the PVC UV panels and remove any excess water.
- Allow the panels to air dry completely before restoring any items or furniture against them.
3. Additional Tips:
- For stubborn stains or grease marks, you can use a non-abrasive household cleaner suitable for PVC surfaces. Apply the cleaner to a soft cloth or sponge and gently rub the stained area, then rinse thoroughly with clean water.
- Avoid using abrasive materials such as steel wool or rough scouring pads, as they can scratch the surface of the PVC UV panels.
- Regular cleaning helps maintain the appearance and durability of the panels. Aim to clean them periodically, depending on how frequently they are exposed to dirt or dust.
- If your PVC UV panels have seams or joints, ensure these areas are cleaned and dried thoroughly to prevent moisture buildup, which can lead to mold or mildew.
Which colors are best selling in uv pvc marble sheet panel ?
The popularity of colors in UV PVC marble sheet panels can vary based on current design trends, regional preferences, and the specific application. However, some colors consistently remain popular due to their versatility, timeless appeal, and ability to complement various interior styles. Here are some of the best-selling colors for UV PVC marble sheet panels:
1. Classic White and Off-White
- White Carrara Marble:
- Mimics the look of Carrara marble with subtle gray veining on a white background. It’s a timeless choice that offers elegance and versatility, fitting well in both modern and classic interiors.
- Calacatta Gold:
- Features a white background with thicker, more pronounced gold or gray veining. This style adds a touch of luxury and is often chosen for its dramatic, high-contrast look.
- Off-White / Cream:
- Off-white or cream panels provide a softer, warmer alternative to pure white, suitable for creating cozy and inviting spaces.
2. Shades of Gray
- Light Gray:
- Light gray panels with subtle veining provide a modern and sleek appearance. They are popular for contemporary kitchens and bathrooms, offering a neutral base that pairs well with various color schemes.
- Dark Gray / Graphite:
- Dark gray or graphite marble panels are chosen for their bold and sophisticated look. They create a striking contrast in light-colored interiors and add depth to design schemes.
3. Beige and Taupe
- Beige:
- Beige panels with delicate veining are a classic choice for traditional and transitional interiors. They bring warmth and a natural feel, making them ideal for living rooms and dining areas.
- Taupe:
- Taupe offers a more modern take on neutral tones, blending gray and beige for a versatile color that complements a wide range of furniture and decor styles.
4. Black and Dark Tones
- Black with White Veining (Nero Marquina):
- Black marble panels with contrasting white veining are chosen for their bold, dramatic effect. They are often used in high-end designs and luxury settings to create a stunning focal point.
- Charcoal:
- A softer alternative to pure black, charcoal panels provide a rich, deep color that adds sophistication without being overpowering.
5. Earthy Browns
- Brown Marble:
- Brown panels with veins in various shades can mimic the look of traditional marble like Emperador. They bring warmth and a natural elegance, fitting well in rustic or classic interiors.
- Chocolate Brown:
- Darker brown panels offer a rich, luxurious look and are often used in spaces where a warm, inviting atmosphere is desired.
6. Unique and Trendy Colors
- Blue Marble:
- Blue marble panels with subtle veining are a unique choice that adds a refreshing and tranquil vibe to spaces. They are popular in coastal and modern designs.
- Green Marble:
- Green panels provide a luxurious and exotic look, often chosen for statement pieces or to add a touch of nature-inspired elegance.
Popular Trends:
- Neutral Colors: Neutrals like white, gray, and beige remain the most popular because they blend seamlessly with various decor styles and color schemes.
- High Contrast: Panels with bold contrasts, such as black with white veining, are trending for their dramatic and sophisticated appearance.
- Warm Tones: Beige, taupe, and brown panels are favored for creating warm, inviting spaces.
Choosing the Best Color:
When selecting a color for UV PVC marble sheet panels, consider the following:
- Interior Style: Match the color to the overall design style of the space (e.g., modern, traditional, eclectic).
- Lighting: Consider how the color will interact with the lighting in the room. Lighter colors can make a space feel larger, while darker tones add depth and drama.
- Existing Decor: Choose a color that complements existing furniture, fixtures, and color schemes.
- Purpose: Think about the function of the room and how the color will influence the atmosphere you want to create (e.g., calming, vibrant, elegant).
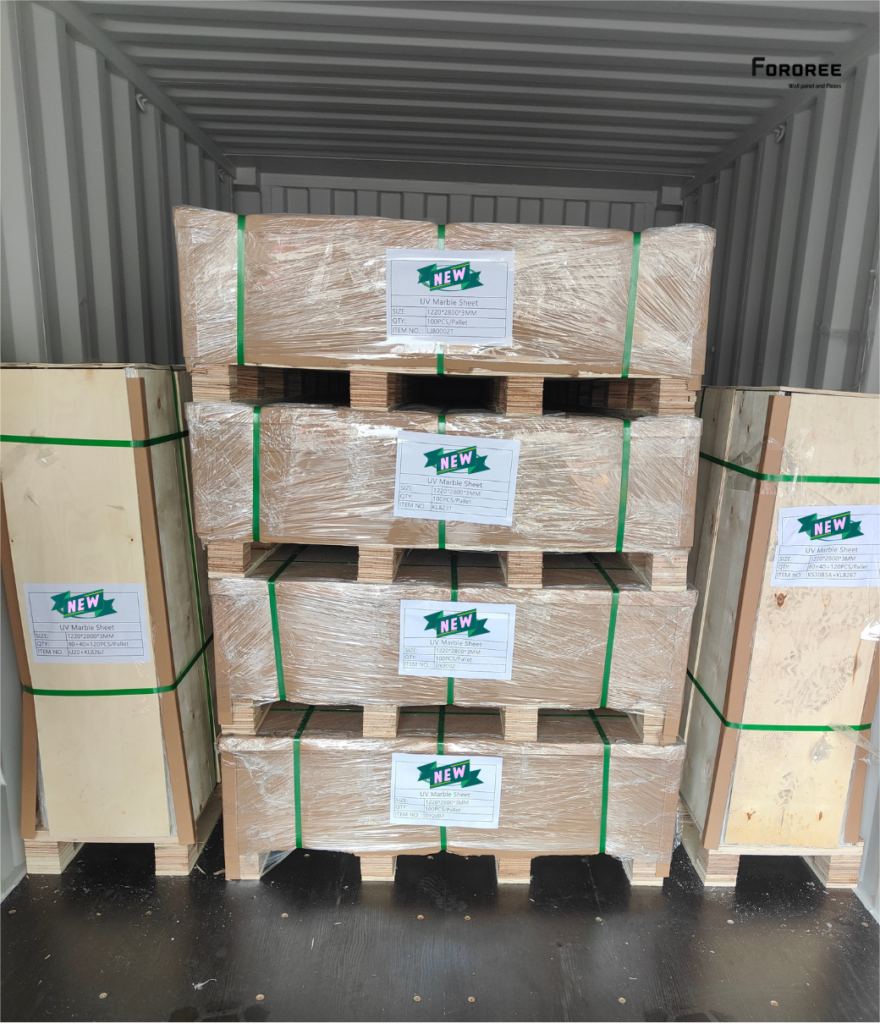
How was the UV marble pvc panel sheet board was packed before loading ?
Proper packaging of UV marble PVC panel sheet boards before loading and shipping is crucial to ensure that they arrive at their destination without damage. Here’s a typical process for packing these panels:
1. Cleaning and Inspection:
- Cleaning: Each panel is thoroughly cleaned to remove any dust or debris that might have accumulated during the production process. This ensures that the panels are pristine before packaging.
- Inspection: Panels are inspected for quality and consistency. Any defective panels are removed from the batch to maintain quality standards.
2. Surface Protection:
- Protective Film: A protective film or sheet is often applied to the surface of each panel to prevent scratches and other surface damage during handling and transportation. This film is typically a peel-off type that the end user can easily remove after installation.
- Corner Guards: Some manufacturers add corner guards to protect the edges and corners of the panels from impacts.
3. Stacking:
- Proper Stacking: Panels are carefully stacked on top of each other. This stacking is usually done in a way that minimizes movement during transport and prevents damage. Panels are often stacked face to face or back to back to protect the finished surfaces.
- Interleaving Material: Soft materials like foam sheets or cardboard are sometimes placed between panels to provide additional cushioning and prevent abrasion.
4. Bundling:
- Strapping: The stacked panels are often bundled together using plastic or metal straps. These straps are secured tightly to keep the panels in place and prevent shifting during transport.
- Shrink Wrapping: For additional security, the bundled stack may be wrapped in shrink film. This keeps the stack together and offers extra protection against dirt, moisture, and minor abrasions.
5. Edge and Corner Protection:
- Edge Protectors: Heavy-duty cardboard or plastic edge protectors may be placed around the edges of the stack to absorb shocks and prevent damage to the edges during handling and transportation.
- Corner Protectors: Similarly, corner protectors are used to safeguard the corners of the stack, which are particularly vulnerable to impacts.
6. Palletizing:
- Pallets: The bundled and protected panels are placed on wooden or plastic pallets for ease of loading and unloading. Pallets also facilitate handling with forklifts and provide stability during transport.
- Securing to Pallets: The panels are secured to the pallets with additional straps or shrink wrap to ensure they do not move during transit.
7. Labeling:
- Identification Labels: Each pallet or bundle is labeled with important information such as product type, dimensions, quantity, handling instructions, and destination details.
- Fragile and Handling Labels: Labels indicating that the panels are fragile and specifying the correct handling orientation (e.g., “This Side Up”) are also applied to the packaging.
8. Loading into Containers or Trucks:
- Careful Placement: When loading onto trucks or shipping containers, the pallets are carefully placed to optimize space and prevent movement during transport.
- Securing in Container: The loaded pallets are often secured within the container using straps, braces, or dunnage (padding materials) to prevent shifting and to absorb shocks and vibrations during transit.
Additional Considerations:
- Climate Control: If the panels are sensitive to extreme temperatures or humidity, consider using climate-controlled transport or adding moisture-absorbing packets within the packaging.
- Shipping Documentation: Proper documentation including packing lists, bills of lading, and any required certifications should accompany the shipment to ensure smooth customs clearance and delivery.
- Insurance: Ensuring the shipment is insured against damage can provide financial protection in case of any incidents during transport.
A 20ft container can load how many pcs of marble UV board panel ?
Due to container weight limit, a 20ft only could load approx 1000-1700pcs based on different size and different weight uv panel, if packed with wooden pallet, any size of the uv marble panel the most only could load between 1000-1200pcs, since wooden pallet will occupy much space.
A 40ft container can load how many pcs of marble UV board panel ?
Compare with 20ft or 40ft, since container loading has limit of weight, so the uv sheet loading quantity is nearly similar to 20ft, But, there will be a huge volume rest in the 40HQ container, in that case, insert the new wall decoration material PU STONE PANEL would be a smart choice, since it’s light weight and a bit big,only after loading them together, the sea cost could be balanced, the PU STONE like was FREE of charge ! It’s an amazing thing, isn’t it ?
Get the latest E-catalogue and Price list from W.a: +8619817731588