What is UV panel ?
A UV board panel, also known as a UV-coated board panel, is a type of panel that is coated with a layer of UV-cured resin or paint. This coating provides a high-gloss finish and a smooth surface, which makes the panel both aesthetically appealing and durable. UV board panels are commonly used in interior design and furniture making due to their attractive appearance and resistance to wear and tear.
The UV coating process involves applying a special resin to the panel and then exposing it to ultraviolet (UV) light. The UV light cures the resin quickly, creating a hard, protective layer on the surface. This coating can protect the panel from scratches, moisture, and other types of damage, and it can also enhance the color and finish of the panel.
UV board panels are often used for kitchen cabinets, wardrobes, furniture, wall paneling, and other interior applications where a glossy, smooth finish is desired. They are available in various colors, patterns, and textures to suit different design preferences.
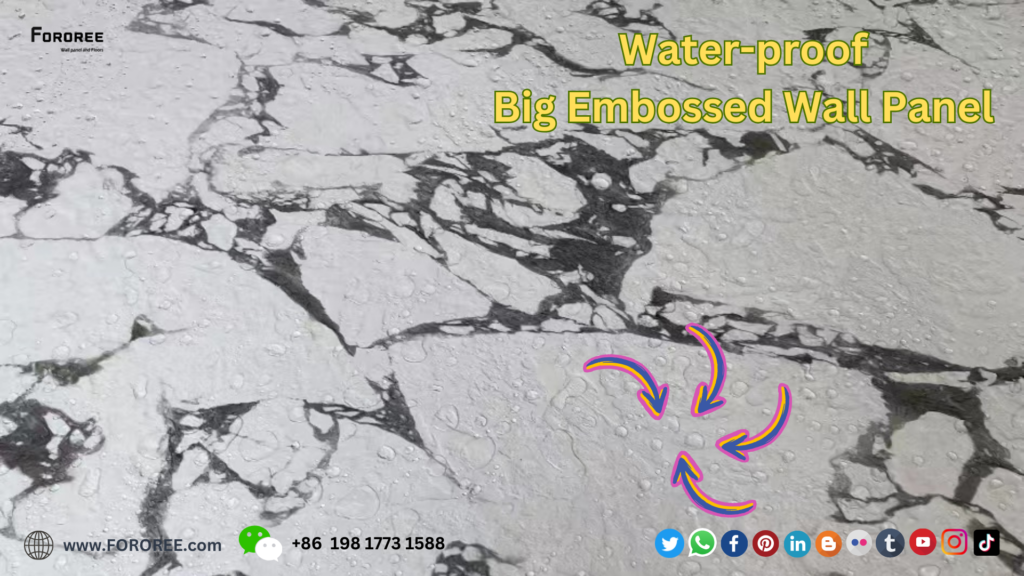
What is the speciication of UV board panel?
UV board panels are typically made from a substrate material, such as medium-density fiberboard (MDF) or plywood, and coated with a UV-curable resin or paint. This coating gives the panel its distinctive high-gloss or matte finish, as well as its durability and resistance to wear and tear. The specifications of UV board panels can vary depending on the manufacturer and the specific product. However, here are some general specifications you can expect:
Substrate:
- Material: The most common substrates for UV board panels are MDF, particleboard, or plywood.
- Thickness: The thickness of the panel can vary, typically ranging from 3mm to 25mm, depending on the application and the desired strength.
- Density: The density of the substrate can vary, with higher density materials offering better stability and strength.
UV Coating:
- Type: UV coatings can be either matte or glossy, offering different finishes based on preference and application.
- Thickness: The UV coating is typically thin, but it provides a strong and durable layer on the surface of the panel.
- Colors and Patterns: UV panels come in a wide range of colors and patterns, including solid colors, wood grain patterns, and custom designs.
Size:
- Standard Sheet Size: UV board panels are available in standard sheet sizes, such as 4 feet x 8 feet (1.22 meters x 2.44 meters), though other sizes may also be available.
- Custom Sizes: Some manufacturers may offer custom-sized panels to suit specific project needs.
Durability:
- Scratch Resistance: UV board panels are known for their resistance to scratches, making them suitable for high-traffic areas.
- Moisture Resistance: The UV coating provides moisture resistance, making the panels suitable for use in kitchens and bathrooms.
UV Coating Properties:
- VOC Levels: UV coatings typically have low levels of volatile organic compounds (VOCs), making them a more eco-friendly option.
- Curing Time: UV coatings cure quickly under ultraviolet light, speeding up the production process.
Applications:
- Furniture: UV board panels are commonly used in furniture making, such as cabinets, wardrobes, and shelving.
- Interior Design: They are also used in interior design for wall paneling, ceiling designs, and decorative elements.
- Signage: UV panels can be used for signage and displays due to their vibrant colors and smooth finishes.
Other Specifications:
- Edge Banding: UV board panels may be finished with edge banding for a clean, polished look.
- Weight: The weight of UV board panels can vary depending on the substrate and thickness.
Keep in mind that specific UV board panel products may have additional specifications based on the manufacturer and the intended use of the panel. Always refer to the manufacturer’s technical data sheet for precise details about the product you are considering.
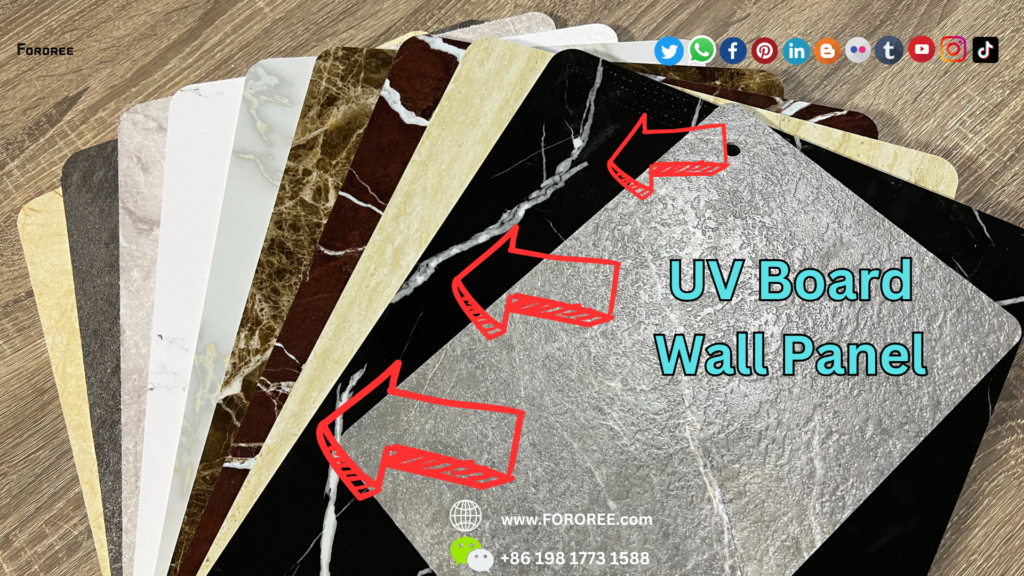
UV board advantage and disadvantage
UV board panels, also known as UV-coated panels, have several advantages and disadvantages depending on the specific application and user preferences. Here are some of the key points:
Advantages:
- High Gloss Finish: UV board panels offer a high-gloss finish that enhances the aesthetic appeal of furniture and interiors.
- Durability: The UV coating provides excellent protection against scratches, moisture, and general wear and tear, making the panels more durable and long-lasting.
- Color Vibrancy: UV coating enhances the vibrancy and depth of colors, making the panels visually appealing.
- Resistance to Fading: The UV-coated surface is resistant to fading due to exposure to sunlight or UV light.
- Easy to Clean: The smooth, glossy surface of UV board panels makes them easy to clean and maintain.
- Eco-Friendly: UV coatings are generally low in volatile organic compounds (VOCs), which makes them more environmentally friendly compared to some other finishes.
- Variety: UV board panels come in a wide range of colors, textures, and patterns, providing a lot of design options.
Disadvantages:
- Cost: UV board panels can be more expensive than other types of panels due to the additional UV coating process.
- Repair Difficulty: If the UV-coated surface is damaged (e.g., chipped or scratched), it can be challenging to repair or touch up without affecting the appearance of the panel.
- Limited Flexibility: UV board panels are usually rigid and may not be suitable for applications that require bending or shaping.
- Glare and Reflection: The high-gloss finish can create glare and reflection under certain lighting conditions, which may not be desirable in some environments.
- Not Heat Resistant: UV board panels may not be highly resistant to heat, so they are not ideal for applications where they will be exposed to high temperatures.
- Installation Challenges: Due to the glossy surface, UV board panels may require special care during installation to avoid scratches and blemishes.
When considering UV board panels, it’s essential to weigh these advantages and disadvantages against your specific project needs and preferences.
Matte UV board vs glossy uv board
UV board panels are available in different finishes, including matte and glossy. Each finish offers distinct advantages and disadvantages depending on the desired aesthetic and functional requirements of a project. Let’s compare matte and glossy UV board panels:
Matte UV Board
Advantages:
- Reduced Glare: Matte finishes have a lower level of reflectivity, making them suitable for spaces with bright lighting or direct sunlight, as they help reduce glare.
- Subtle Appearance: Matte UV board panels provide a more understated, elegant look that blends well with modern and minimalist design styles.
- Conceals Imperfections: The matte surface tends to conceal minor scratches, fingerprints, and dust more effectively than glossy surfaces.
- Smooth Touch: The matte finish offers a smooth, soft touch and may feel more comfortable to the touch for some people.
- Less Maintenance: Since matte UV board panels show fewer smudges and fingerprints, they may require less frequent cleaning.
Disadvantages:
- Less Vibrant Colors: The matte finish can dull colors slightly compared to the glossy finish, making them appear less vibrant.
- Less Resistance to Wear: Matte UV boards may be more prone to scratches and wear compared to glossy boards.
- Harder to Clean Stains: While fingerprints may be less noticeable, certain stains or spills may be harder to clean on matte surfaces.
Glossy UV Board
Advantages:
- High Gloss Finish: Glossy UV board panels provide a shiny, reflective surface that enhances the overall aesthetic appeal and makes colors more vibrant.
- Durability: The UV coating offers a high level of durability and protection against moisture and scratches.
- Visual Appeal: Glossy finishes can give interiors a luxurious, modern, and high-end look.
- Easy to Clean: The smooth, shiny surface is easy to wipe down and clean.
Disadvantages:
- Glare and Reflection: The high-gloss finish can produce glare and reflection under certain lighting conditions, which may be distracting in some environments.
- Visible Imperfections: Glossy surfaces tend to highlight fingerprints, smudges, and scratches more than matte surfaces.
- Maintenance: Glossy UV boards may require more frequent cleaning to maintain their pristine appearance due to visible fingerprints and smudges.
When choosing between matte and glossy UV board panels, consider the specific use and aesthetics of your project. For example, glossy finishes may be more appropriate for spaces where a luxurious, high-end look is desired, while matte finishes may work better in environments with bright lighting or for a more subtle, contemporary appearance.
How to install UV board panel?
Installing UV board panels can be a straightforward process if you take care to follow the right steps and use the appropriate tools. Here’s a general guide on how to install UV board panels:
Materials and Tools Needed:
- UV board panels
- Measuring tape
- Pencil
- Level
- Cutting tools (e.g., saw, utility knife) for cutting the panels to size
- Drill and screws or adhesive (such as construction adhesive)
- Stud finder (for walls)
- Sandpaper (for smoothing edges)
- Safety equipment (e.g., goggles, gloves)
- Clamps (optional, for securing panels in place while adhesive sets)
Installation Steps:
- Measure the Area:
- Measure the area where you want to install the UV board panels. Use a measuring tape to ensure you get accurate measurements.
- Mark the measurements on the UV board panels using a pencil.
- Cut the Panels:
- Use a saw or utility knife to cut the UV board panels to the required size. Make sure to follow safety precautions when cutting the panels.
- Smooth the cut edges with sandpaper.
- Prepare the Surface:
- Ensure the surface where the panels will be installed is clean, dry, and free of dust and debris.
- If necessary, use a level to check that the surface is even. Make adjustments as needed.
- Plan the Layout:
- Plan the layout of the UV board panels before starting the installation to ensure you achieve the desired look and minimize waste.
- Mark the wall or installation surface with a pencil to indicate where the panels will be placed.
- Install the Panels:
- With Adhesive: Apply construction adhesive to the back of the UV board panel. Place the panel onto the wall or surface and press firmly to ensure a strong bond. Use clamps to hold the panel in place if necessary while the adhesive sets.
- With Screws: Drill pilot holes into the UV board panel and the installation surface. Attach the panel to the wall or surface using screws. Be careful not to overtighten the screws, as this can cause damage to the panel.
- Check Alignment:
- Use a level to ensure each panel is installed straight and level. Make adjustments as needed during the installation process.
- Install Remaining Panels:
- Continue installing the remaining panels in a similar manner, ensuring that each panel is aligned with the others.
- Finish Edges and Joints:
- Depending on the look you want, you may want to use trim or molding to finish the edges and joints between panels.
- If using trim, attach it to the wall using adhesive or nails.
- Clean Up:
- Once the installation is complete, clean up any debris and tools used during the process.
- Check the installation area to make sure everything looks neat and professional.
With these steps, you should be able to successfully install UV board panels. Keep in mind that specific installation details may vary depending on the type of panels and the surface being installed. Always follow the manufacturer’s instructions for best results.
UV board panel match to which wall decoration material mostly
UV board panels can complement a variety of wall decoration materials, depending on the design style you are aiming for. Their high-gloss or matte finish provides a sleek and modern appearance, making them versatile in matching different materials. Here are some wall decoration materials that UV board panels can match well with:
- Paint:
- UV board panels can be used as accent pieces against painted walls. Depending on the color and finish, they can create contrast or harmony with the paint color.
- Wallpaper:
- Wallpaper can offer textures, patterns, and colors that complement the UV board panels. UV boards can serve as feature panels, adding a focal point against wallpapered walls.
- Wood Paneling:
- If you choose a wood finish for the UV board, it can blend seamlessly with wood paneling for a natural and cohesive look. Alternatively, contrasting finishes can add visual interest.
- Tile:
- UV board panels can be installed adjacent to tile walls, particularly in areas like kitchens and bathrooms, to add a glossy, modern touch. They can provide a contrasting finish and texture to tiles.
- Stone:
- UV board panels can create a striking visual contrast when paired with stone walls or stone-like textures. The combination of natural and synthetic materials can create a dynamic and contemporary look.
- Brick:
- UV board panels can offer a sleek and modern contrast against rustic brick walls. The juxtaposition of smooth panels and rough brick can add character to a room.
- Glass:
- UV board panels can match well with glass elements, such as glass tiles or partitions. The reflective qualities of glass and UV panels can create a cohesive modern aesthetic.
When matching UV board panels with other wall decoration materials, consider the overall design theme, colors, and textures to achieve a harmonious or contrasting look based on your preferences. You may also want to take into account the lighting in the room, as it can influence the appearance of both the UV panels and the wall decoration materials.
Does uv board expensive ?
The cost of UV board panels can vary depending on several factors, including the quality of the UV coating, the type of substrate (e.g., MDF, plywood), the finish (matte or glossy), the size and thickness of the panels, and the manufacturer. In general, UV board panels may be more expensive than standard panels without UV coating due to the additional manufacturing process and the quality of the finish.
Factors Influencing Cost:
- Quality of UV Coating: Higher-quality coatings may come at a premium but can offer better durability and finish.
- Type of Substrate: Different substrates (e.g., MDF, plywood) have different costs, with some being more expensive than others.
- Finish: Glossy finishes can sometimes be more costly than matte finishes due to the additional processes involved in achieving the high-gloss surface.
- Size and Thickness: Larger and thicker panels may cost more due to the additional material used.
- Manufacturer: Brand reputation, manufacturing techniques, and geographic location can all affect the price of UV board panels.
- Customization: If you require custom colors, patterns, or designs, it may add to the overall cost.
Cost Considerations:
- While UV board panels may be more expensive upfront, their durability and low maintenance needs could make them a cost-effective choice in the long run.
- When considering the cost of UV board panels, also take into account the benefits they provide, such as high durability, ease of cleaning, and aesthetic appeal.
Overall, UV board panels are not necessarily prohibitively expensive, but they are an investment in terms of quality and appearance. It’s worth comparing prices and options from different suppliers to find the best fit for your project and budget. Additionally, consider the long-term benefits of UV board panels, such as their durability and aesthetic qualities, when evaluating the overall cost.
What kind of machine produce UV panel
The production of UV-coated panels (commonly referred to as UV panels or UV boards) involves a series of processes and machines that work together to apply a UV-cured finish to a base panel. Here are some of the key machines and equipment used in the production of UV panels:
- Substrate Preparation Machines:
- Sanding Machine: Used to prepare the surface of the substrate (e.g., MDF, plywood) by smoothing it and removing any imperfections to ensure proper adhesion of the UV coating.
- Dust Collector: Removes dust and debris from the panel to ensure a clean surface for coating.
- Coating Application Machines:
- Roller Coater: Applies a uniform layer of UV-curable coating onto the surface of the panel. Different types of rollers may be used depending on the desired finish (e.g., matte, glossy).
- Spray Coater: Another method for applying UV-curable coating. Spray coating can provide a more even and controlled application in some cases.
- UV Curing Machines:
- UV Oven: After the coating is applied, the panels are conveyed through a UV oven where they are exposed to UV light. The UV light cures the coating almost instantly, creating a hard, durable surface.
- Conveyor Belt: Moves the panels through the UV curing process at a consistent speed.
- Cooling Equipment:
- Cooling Tunnel: Once the panels have been cured, they may be passed through a cooling tunnel to bring the temperature down and stabilize the coating.
- Quality Control Equipment:
- Inspection Station: After the panels are produced, they are inspected for quality. This may include visual inspections and automated systems to check for defects.
- Cutting and Finishing Machines:
- Panel Saw: Used to cut the panels to the desired size and shape.
- Edge Banding Machine: If necessary, edge banding machines can apply edge treatments to the UV panels for a finished look.
These machines work together in a production line to produce UV-coated panels efficiently and with high precision. Manufacturers often customize their production lines based on the specific types of panels they produce and the desired finishes and effects.
UV painting step is very important for a uv board panel
Yes, the UV painting or coating step is a crucial part of the production process for UV board panels. It plays a significant role in determining the final appearance, durability, and quality of the panels. Here are some key points about the importance of the UV painting step:
- Appearance:
- The UV coating gives UV board panels their distinctive glossy or matte finish, enhancing their aesthetic appeal and making them visually attractive.
- Protection:
- UV coating provides a protective layer that guards the panel against scratches, moisture, and general wear and tear. This makes the panel more durable and long-lasting.
- Color Enhancement:
- The UV coating can intensify the colors of the underlying panel, making them more vibrant and striking.
- Smooth Finish:
- UV coating creates a smooth, even surface on the panel, which is key for achieving the desired look and ensuring that the panel is easy to clean.
- Rapid Curing:
- UV coating cures quickly under ultraviolet light, which speeds up the production process and allows for efficient mass production of UV board panels.
- Adhesion:
- Proper application and curing of the UV coating ensure strong adhesion to the substrate, which is essential for the panel’s longevity and resistance to damage.
- Customization:
- UV painting allows for a variety of finishes, including different colors, patterns, and effects. This provides versatility in terms of design and customization options.
Given these benefits, the UV painting step is a critical part of the manufacturing process for UV board panels. It is important to apply the coating evenly and correctly to achieve the desired finish and quality. The use of high-quality UV-curable paints and coatings, as well as precise application techniques, is essential for producing panels that meet customer expectations and industry standards.
Which country or areas like UV sheet panel most
UV sheet panels, also known as UV board panels, are popular in various parts of the world due to their aesthetic appeal, durability, and versatility in design. While they are used in many countries, their popularity can vary based on regional design trends, economic factors, and the availability of manufacturing infrastructure. Here are some areas where UV sheet panels are particularly popular:
- China:
- China is one of the largest producers of UV sheet panels, and they are widely used in the country’s growing construction and interior design industries.
- The variety of colors, patterns, and finishes available makes UV panels a popular choice in residential and commercial projects.
- India:
- UV sheet panels are increasingly popular in India due to their aesthetic appeal and durability. They are used in a variety of applications, including kitchen cabinets, furniture, and interior design.
- The panels’ glossy and matte finishes align well with modern and contemporary design trends in the country.
- Southeast Asia:
- Countries such as Malaysia, Indonesia, and Vietnam have a growing demand for UV sheet panels in residential and commercial projects.
- The panels are used in furniture manufacturing and interior design, offering modern and stylish options for customers.
- Middle East:
- UV sheet panels are used in Middle Eastern countries for their high-end appearance and resistance to wear and tear in the region’s harsh climate.
- They are commonly found in luxury projects, commercial spaces, and upscale residential properties.
- Europe:
- UV sheet panels are used in European countries, especially in modern and contemporary interior design projects.
- The focus on sustainability and eco-friendly materials in some European countries aligns with the use of UV coatings that are low in volatile organic compounds (VOCs).
- North America:
- In the United States and Canada, UV sheet panels are used in furniture and interior design for their aesthetic appeal and ease of maintenance.
- They are particularly popular for kitchen and bathroom cabinetry.
In general, UV sheet panels are well-received in markets where there is a demand for modern design, durable materials, and low-maintenance surfaces. As the global interior design and construction industries continue to evolve, the popularity of UV sheet panels is likely to expand further.
UV panel sheet best selling color
The best-selling color for UV panel sheets can vary depending on current design trends, regional preferences, and the specific application for which the panels are being used. However, there are a few colors that tend to be popular consistently across different markets:
- White:
- White UV panel sheets are very popular because they offer a clean, modern, and versatile look that can match any design style.
- They are often used in kitchens, bathrooms, and other areas where a bright, spacious appearance is desired.
- Grey:
- Shades of grey, from light to dark, are also popular as they offer a sophisticated and contemporary look.
- Grey UV panels can be paired with a variety of other colors and materials, making them a versatile choice for designers.
- Black:
- Black UV panel sheets are commonly used for their bold and elegant appearance.
- They can create a striking contrast with other colors and materials in a space.
- Wood Finishes:
- UV panels with wood grain patterns or finishes are popular in many regions for their natural and warm appearance.
- These panels are often used in furniture, cabinetry, and interior design to achieve a wood-like look with the benefits of UV coating.
- Neutral Tones:
- Neutral tones such as beige, taupe, and soft browns are widely used because they blend well with various design styles and color palettes.
- These colors provide a warm, inviting feel to interiors.
- Pastel Colors:
- Soft pastel colors, such as light blue, pink, or green, can be popular choices for certain applications like children’s rooms or spaces that aim for a softer, more delicate aesthetic.
While these colors are commonly in demand, trends can change over time, and new color preferences may emerge based on design movements, regional cultural influences, and customer tastes. Additionally, some manufacturers offer custom color options to cater to specific preferences and design projects.
How to produce panel UV board
Producing UV board panels involves a series of manufacturing processes that include preparing the substrate, applying a UV-curable coating, and curing the coating using ultraviolet (UV) light. The result is a panel with a smooth, durable finish that can be either high-gloss or matte. Here is an overview of the production process for UV board panels:
Materials and Equipment Needed:
- Substrate Material: Common options include medium-density fiberboard (MDF), particleboard, or plywood.
- UV-Curable Resin or Paint: The coating material that cures under UV light.
- Coating Application Equipment: Machines such as roller coaters or spray coaters for applying the UV coating.
- UV Curing Oven: A machine that exposes the coated panels to UV light, curing the coating quickly.
- Sanding Machines: For preparing the substrate and finishing the panels.
- Cooling Tunnel: To cool down the panels after curing.
- Cutting and Finishing Machines: Panel saws and edge banding machines for cutting the panels to size and applying edge treatments.
Production Process:
- Substrate Preparation:
- Sanding: Begin by sanding the substrate material (e.g., MDF or plywood) to create a smooth surface. This helps the UV coating adhere better.
- Cleaning: Remove any dust and debris from the substrate to ensure a clean surface for coating.
- Coating Application:
- Applying the Coating: Use a roller coater or spray coater to apply a uniform layer of UV-curable resin or paint to the surface of the substrate.
- Quality Control: Check the coating for consistency and uniformity. Adjust the application as necessary.
- UV Curing:
- UV Light Exposure: Pass the coated panels through a UV curing oven, where they are exposed to UV light. The UV light cures the coating almost instantly, creating a hard, durable surface.
- Cooling: After curing, the panels may be passed through a cooling tunnel to stabilize the coating.
- Cutting and Finishing:
- Cutting: Cut the panels to the desired size using a panel saw.
- Edge Finishing: If necessary, apply edge banding to the panels to give them a finished look. This can be done using an edge banding machine.
- Quality Inspection:
- Inspect the Panels: Check the finished panels for quality, including the appearance of the coating, consistency of color, and absence of defects.
- Storage and Shipping:
- Storage: Store the finished UV board panels in a clean, dry environment until they are ready for shipping.
- Shipping: Prepare the panels for shipping to customers or distribution centers.
Safety and Environmental Considerations:
- Safety: Ensure that safety protocols are followed during production, including proper handling of UV-curable resins and use of personal protective equipment (PPE).
- Environmental Impact: Consider the environmental impact of the production process, including waste management and the use of eco-friendly materials.
By following these steps, manufacturers can produce high-quality UV board panels that meet industry standards and customer expectations.