PU Stone Panel China Haining Supplier and manufacturer
PU Stone China Supplier. FOROREE, a pioneering brand in the realm of PU(Polyurethane) Stone Panels,Simulation stone panel,also called faux stone panel, redefining the landscape of interior design with innovation and elegance. With a commitment to excellence, FOROREE combines cutting-edge technology with meticulous craftsmanship to produce premium-quality PU stone panels that exude the authentic charm of natural stone.

Our extensive range of designs and textures offers limitless possibilities for architects, designers, and homeowners alike, empowering them to realize their creative visions with ease. From classic to contemporary, FOROREE’s diverse collection caters to every aesthetic preference, ensuring that each space is imbued with sophistication and character.
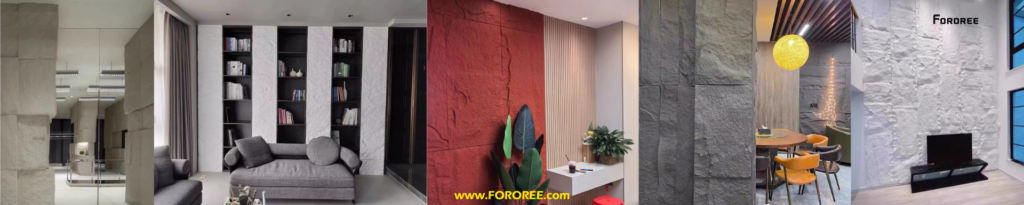
Backed by a dedication to sustainability, FOROREE employs eco-friendly practices throughout its manufacturing process, prioritizing environmental responsibility without compromising on quality. Discover the transformative power of FOROREE PU stone wall panels and elevate your interiors to new heights of beauty and distinction.
Item | Specification |
Type | PU Stone Panel |
Size ( L*W*H ) | 1200*600*(20-100)mm |
Color | pure white, milk white, drak, grey, beige, light grey, blue, LV red |
Features | lightweight, easy transportation, fast installation, fireproof, waterproof |
Light Weight | 1.5-3kgs/pc |
Fireproof | B1 |
Application | interior wall, exterior wall |
Packing | pearl wool or bubble bag, solid carton, plastic pallet |
Installation | glue and nail |
MOQ | 100pcs |
Service Life | more than 20 years |
What we offer ?
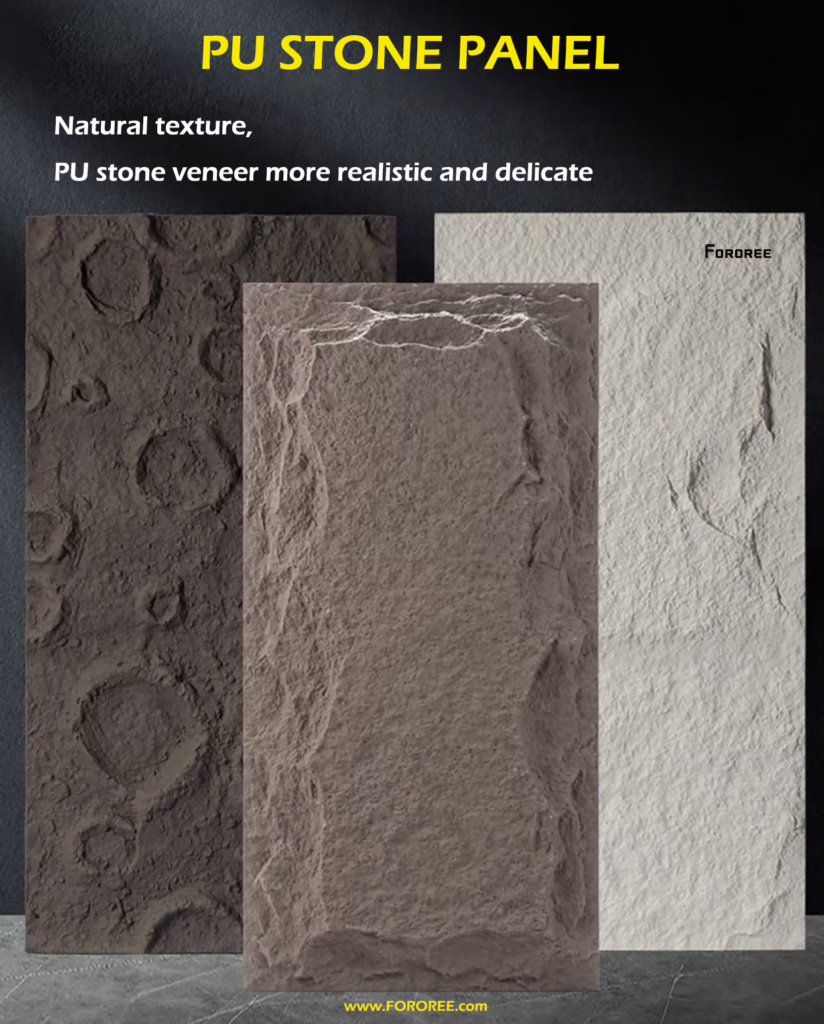
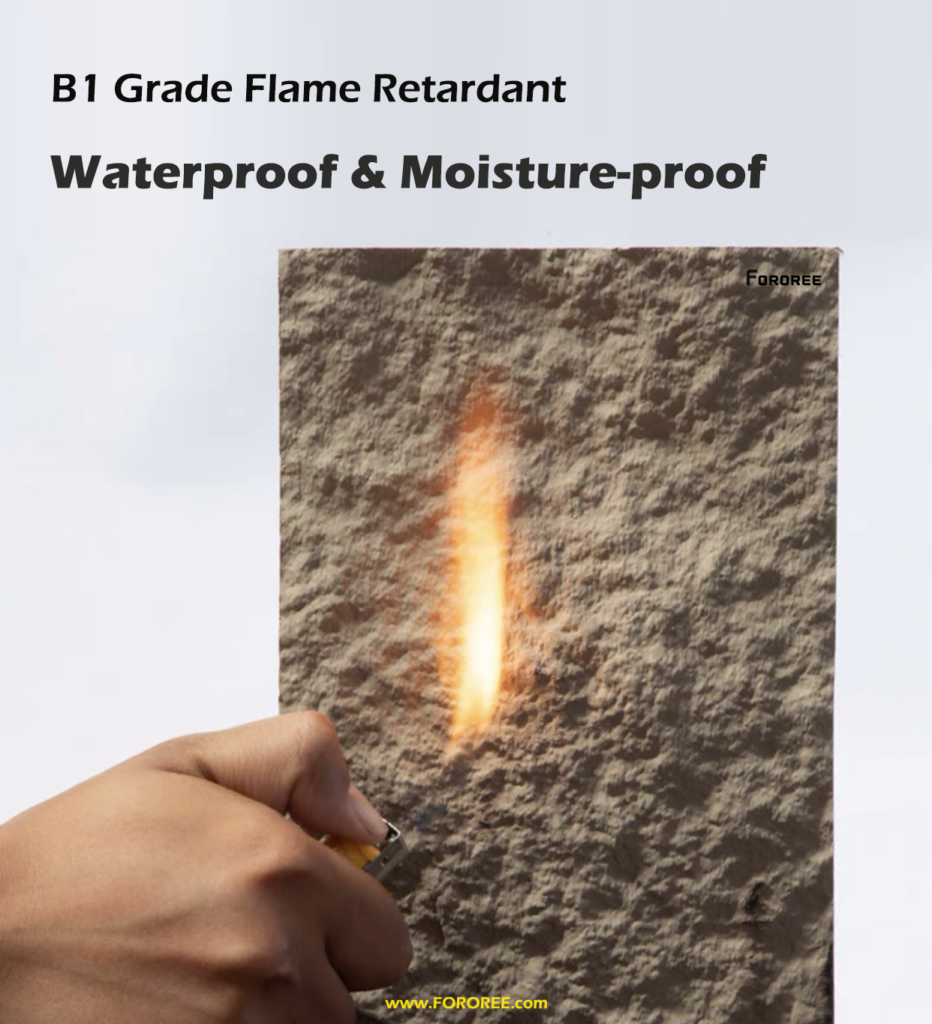



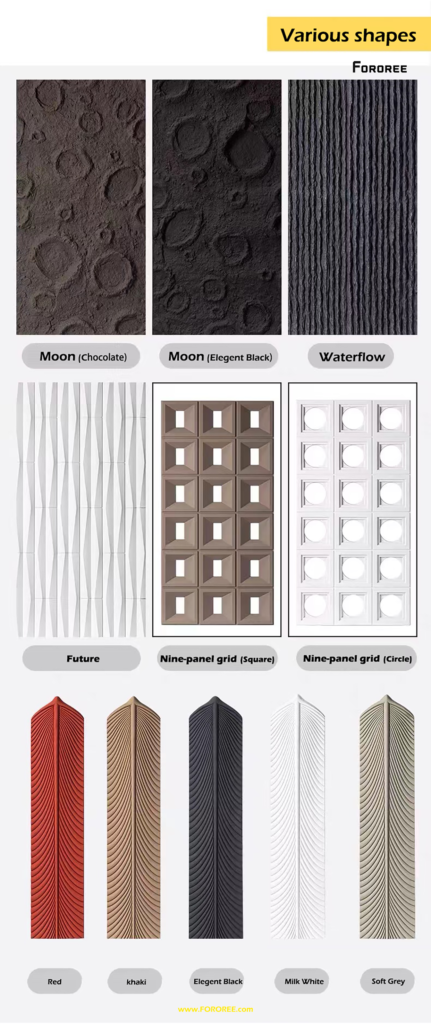

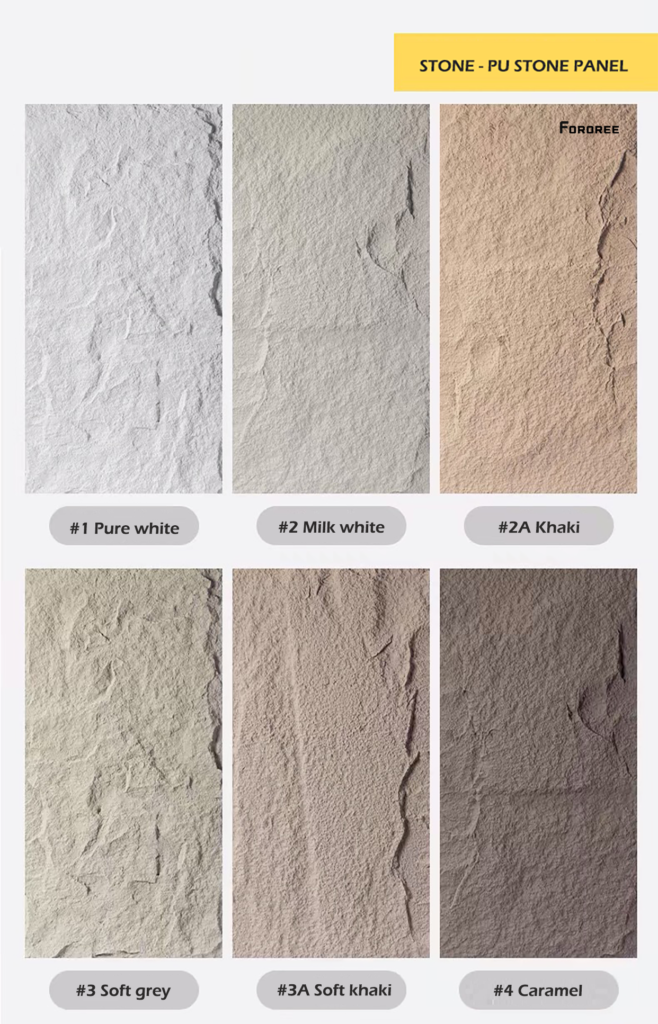
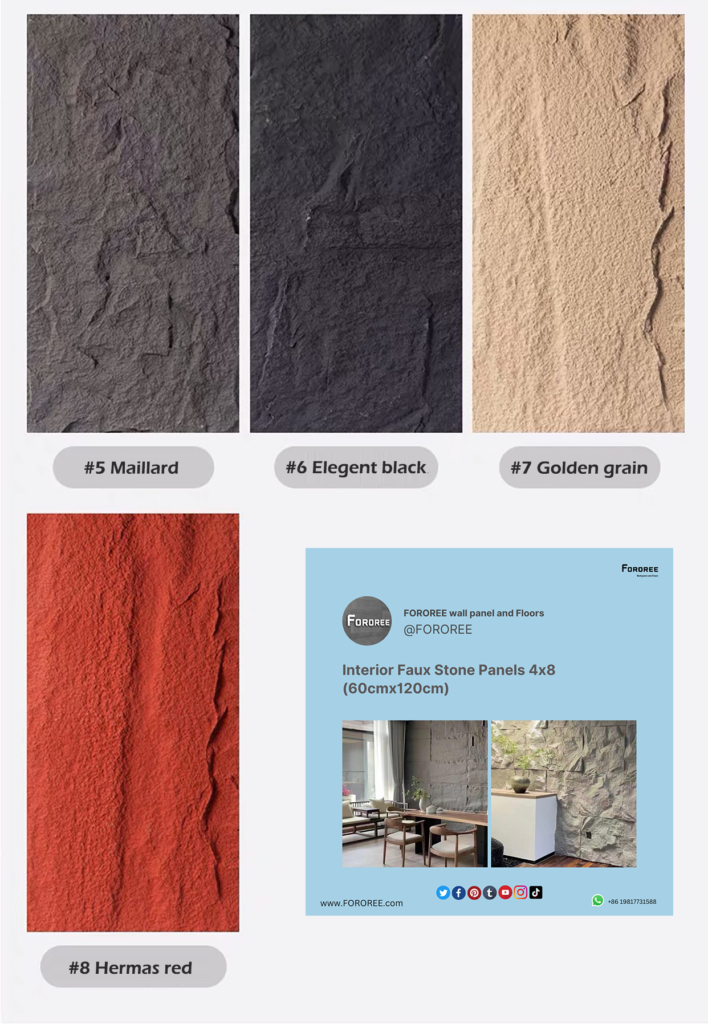


How are so many beautiful PU stone panels produced?
The production of beautiful PU stone panels involves a meticulous process that combines advanced technology with skilled craftsmanship. At Fororee, our panels begin with the careful selection of high-quality raw materials, including polyurethane resin, fillers, pigments, and additives. These materials are precisely mixed to achieve the desired color and texture, ensuring consistency and vibrancy across each panel.
Next, our expert craftsmen utilize custom-designed molds to shape the PU mixture into stunning stone patterns, meticulously capturing the intricate details and textures found in natural stone. The panels then undergo a curing process to solidify and strengthen the material, resulting in durable yet lightweight panels that are easy to install.

To enhance the visual appeal of our panels, we employ state-of-the-art techniques such as surface finishing and coloring, carefully adding realistic nuances and depth to mimic the natural beauty of stone. Our dedication to quality extends to rigorous quality control measures, ensuring that each panel meets our exacting standards before it reaches our customers.
What raw materials are used in the PU Stone Panel production?

The production of PU (polyurethane) stone panels typically involves several key raw materials:
- Polyurethane Resin: This is the primary component of PU stone panels. Polyurethane resin serves as the binder that holds the other ingredients together. It provides flexibility, durability, and weather resistance to the finished panels.
- Fillers: Fillers are used to bulk up the mixture and reduce the cost of production. Common fillers include calcium carbonate, talc, or other minerals. These materials help control the density and texture of the final product.
- Pigments: Pigments are added to the mixture to give the panels their desired color. They can range from earthy tones to vibrant hues, allowing for a wide variety of aesthetic options.
- Additives: Various additives may be incorporated to enhance specific properties of the panels, such as UV resistance, flame retardancy, or flexibility. Examples of additives include stabilizers, antioxidants, and flame retardants.
- Release Agents: Release agents are applied to molds to prevent the cured panels from sticking to the mold surfaces. This facilitates easy removal of the panels during the production process.
What kind of machines produced PU Stone Wall Panel?
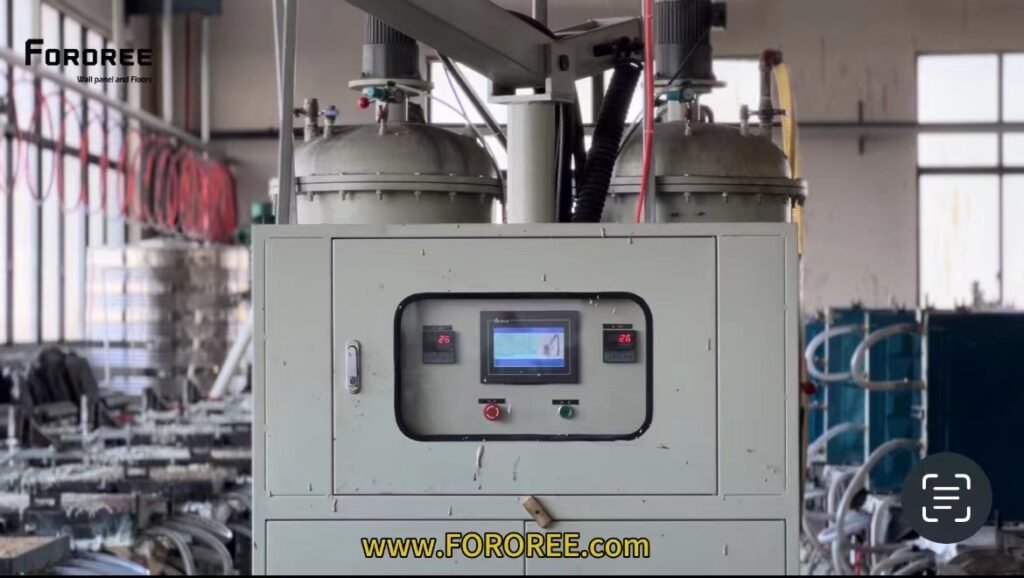
Curing Oven: After the PU material is poured into the molds, it undergoes a curing process to solidify and strengthen the panels. Curing ovens provide controlled heat and airflow to accelerate the curing process and ensure uniform curing throughout the panels.
Trimming Machine: Once the panels are cured, they are removed from the molds and may require trimming to remove any excess material or imperfections. Trimming machines are used to precisely trim the edges of the panels to achieve the desired shape and size.
Surface Treatment Equipment: Surface treatment equipment may include machines for adding texture, applying coatings, or finishing the panels to enhance their appearance and performance. This equipment helps create the desired aesthetic effects and may include tools such as spray guns or rollers.
Quality Control Equipment: Various instruments and tools are used for quality control purposes, including devices for measuring dimensions, testing mechanical properties, and inspecting surface finish. These tools ensure that the finished panels meet the required specifications and quality standards.
How to make / produce PU Stone Panels ?
Relate artical: how-to-install-pu-stone-panel
PU faux stone panel production process
The production process for PU (polyurethane) stone panels typically involves the following steps:
- Material Preparation:
- Raw materials, including polyurethane resin, fillers, pigments, additives, and release agents, are gathered and prepared for mixing.
- Mixing:
- The raw materials are carefully measured and mixed together in specific proportions using mixing equipment. This creates a homogenous mixture that will form the base material for the panels.
- Molding:
- Custom-designed molds, often made of silicone or other materials, are prepared to replicate the desired texture and appearance of natural stone.
- The mixed PU material is poured into the molds, ensuring even distribution and complete filling of the mold cavities.
- Curing:
- The filled molds are placed in a curing chamber or oven where the PU material is allowed to cure and solidify. Curing times may vary depending on factors such as temperature, humidity, and the specific formulation of the polyurethane.
- Demolding:
- Once cured, the solidified PU stone panels are removed from the molds. Careful attention is paid to avoid damaging the panels during demolding.
- Trimming and Finishing:
- Any excess material or imperfections on the edges of the panels are trimmed to achieve the desired shape and size.
- Surface treatments, such as adding texture or applying coatings, may be performed to enhance the appearance and performance of the panels.
- Quality Control:
- The finished panels undergo rigorous quality control inspections to ensure they meet the required standards for strength, durability, appearance, and safety.
- Defective panels are identified and either repaired or discarded to maintain product quality.
- Packaging and Distribution:
- The finished PU stone panels are packaged and prepared for shipment to customers. Proper packaging is essential to protect the panels during transit and storage
How is a fast realistic and high quality PU stone produced and made?
Please see the video highlights below:

Email us:hello@FOROREE.com Whatsapp: +8619817731588